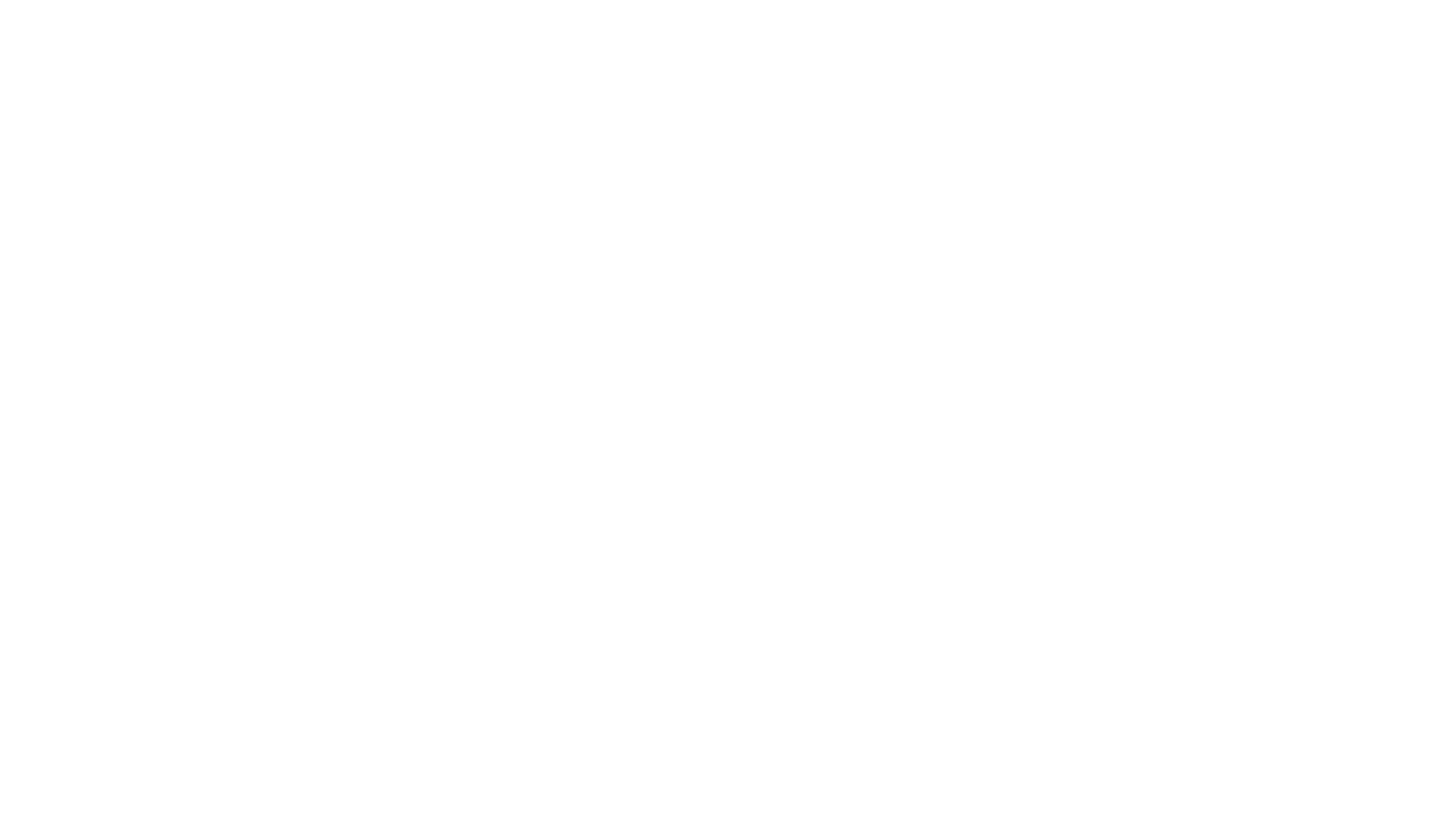
Sulfuric Acid Treatment
Safe and efficient sulfuric acid recovery, purification, and concentration
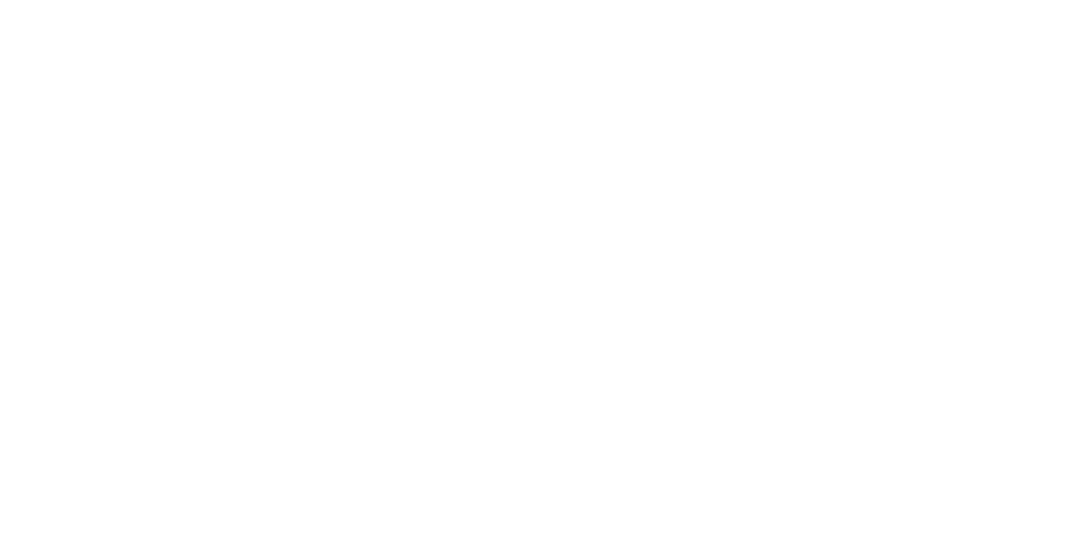
Optimized Sulfuric Acid Management
Sulfuric acid plays a critical role in chemical synthesis, metal processing, and gas drying, but contamination and dilution lead to high disposal costs and environmental challenges. We provide tailored solutions to recover, purify, and concentrate sulfuric acid, ensuring cost savings, process efficiency, and regulatory compliance.
Performance & Safety
Efficient recovery and reconcentration of sulfuric acid
Corrosion-resistant materials for long-term durability
Vacuum concentration technology to reduce energy costs
Custom solutions for sulfuric acid dilution and reuse
Efficient Recovery & Waste Reduction
We help you recover sulfuric acid from spent process streams, minimizing waste and maximizing resource efficiency. Our advanced vacuum concentration technology enables reconcentration up to 98 % while keeping operating temperatures low, reducing corrosion risks and energy consumption.
Key Applications
Concentration and recovery of spent sulfuric acid
Sulfuric acid purification for battery and electronics industries
Removal of organic contaminants from industrial acids
Dilution and blending for customized acid solutions
Looking for a reliable sulfuric acid recovery solution?
Document to download
Request a download
In order to process your brochure request efficiently, we kindly ask you to provide the required information through our form.