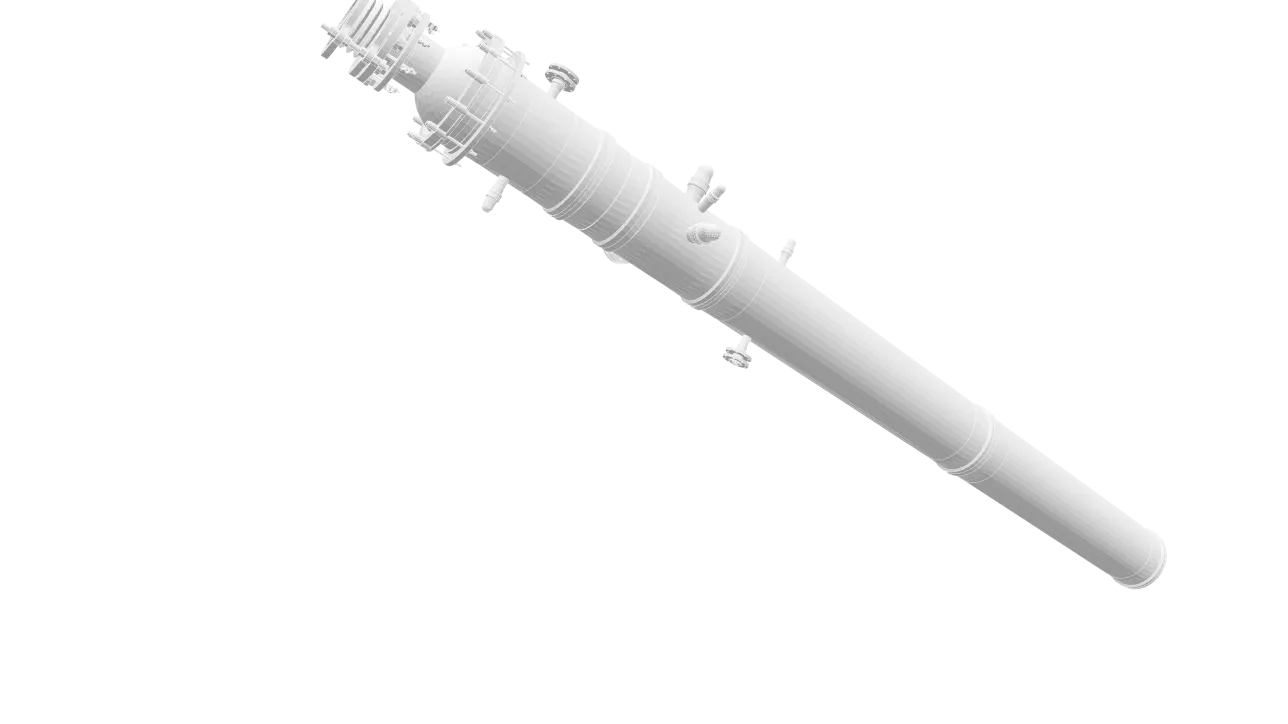
Hero
Distillation
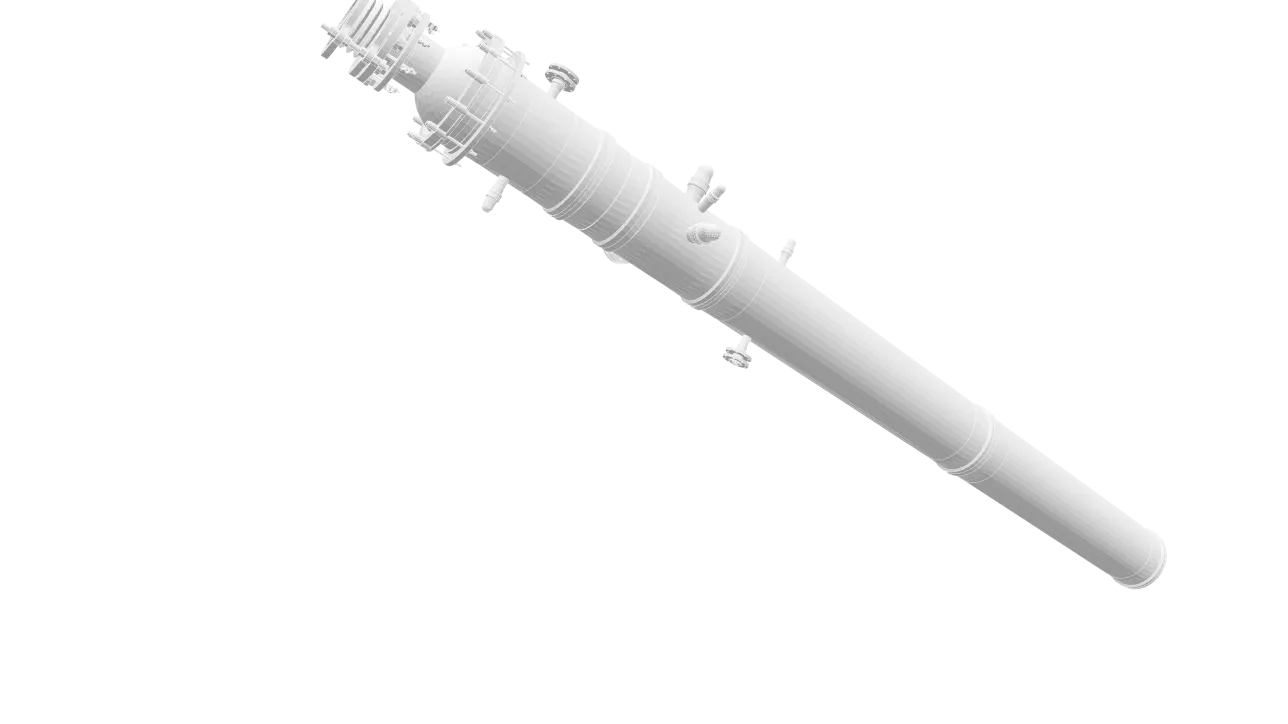
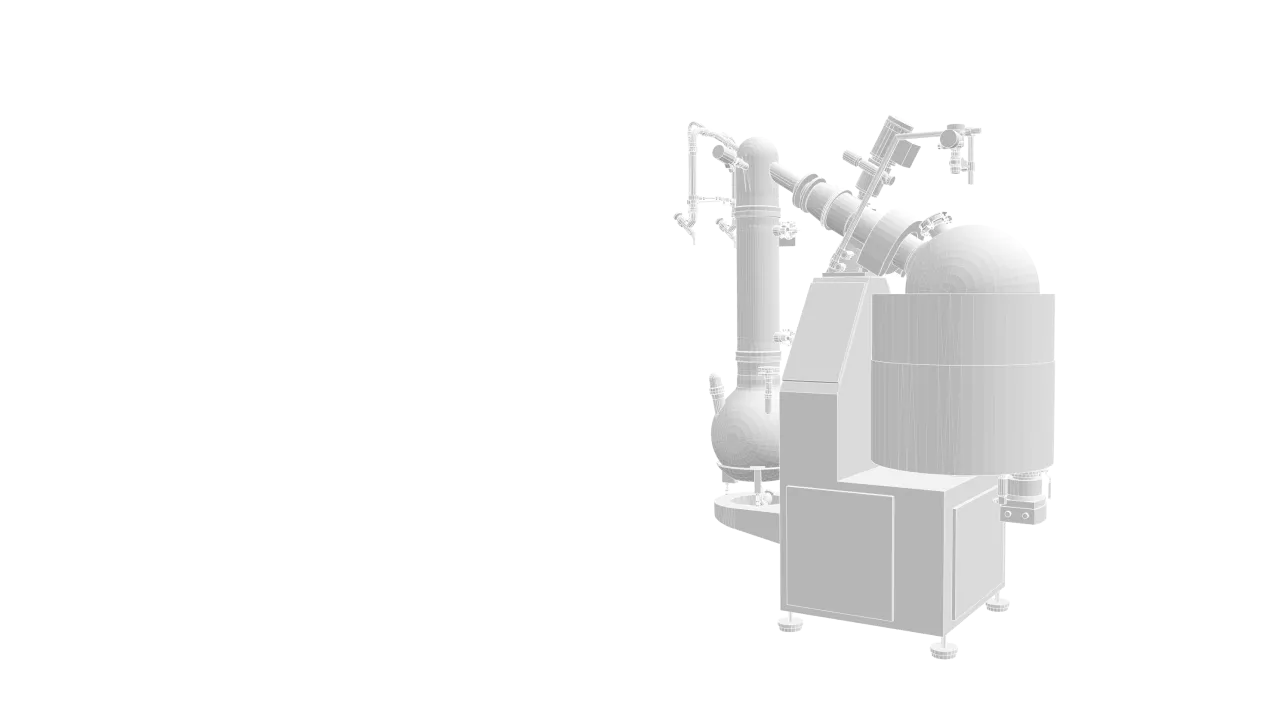
Rotationsverdampfer
QVF® ROTADEST Lösung für Lösungsmittelverdampfung, Kristallisation, Trocknung von Suspensionen, Pulvern oder Granulaten, verschiedene chemische Reaktionen in der Flüssigphase oder im Ex-Bereich
Glas VerdampfungDestillation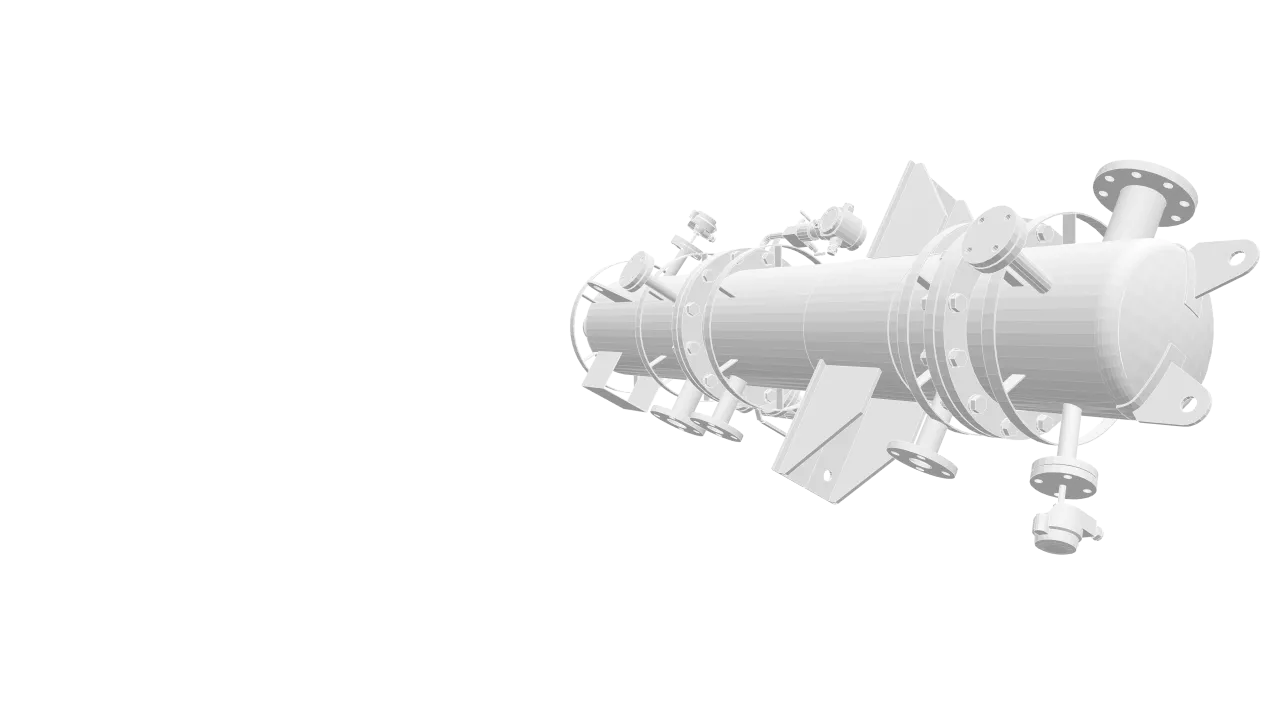
REKTIFIKATIONSTECHNIK
Distillation columns are used when a great number of theoretical stages are required, meaning that when the products to be separated are close in terms of boiling point.
Legierung DestillationVerdampfung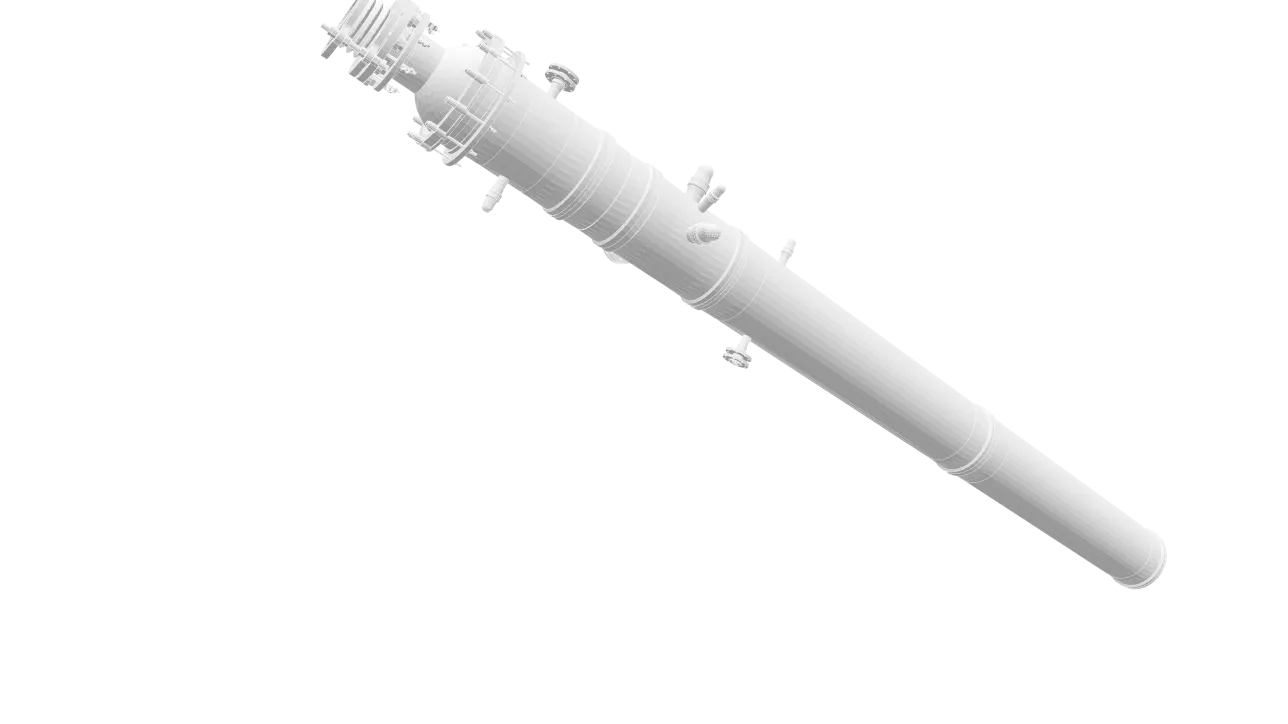
Zwangsumlaufverdampfer
Robuste Ausrüstung für schwierig zu handhabende Prozesse
Legierung DestillationVerdampfung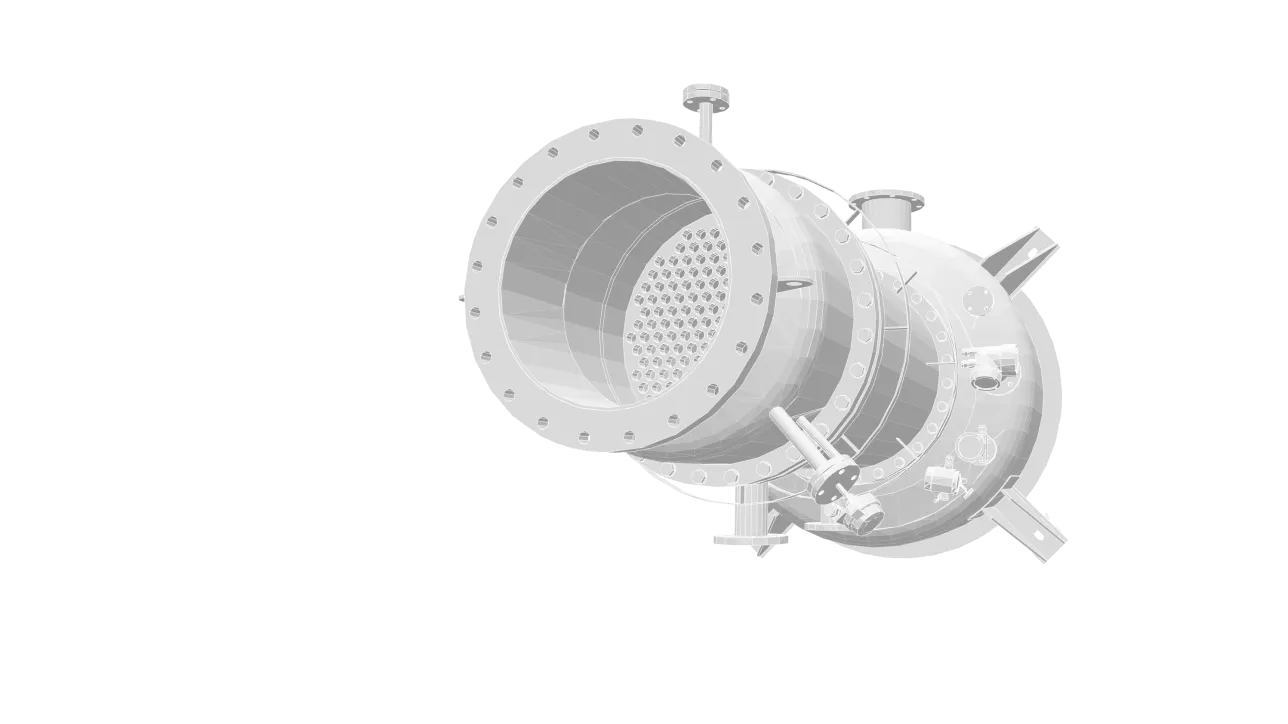
Kurzwegverdampfer
Der Einzigartige Verdampfer Für Außergewöhnliche Anwendungen
Legierung DestillationVerdampfung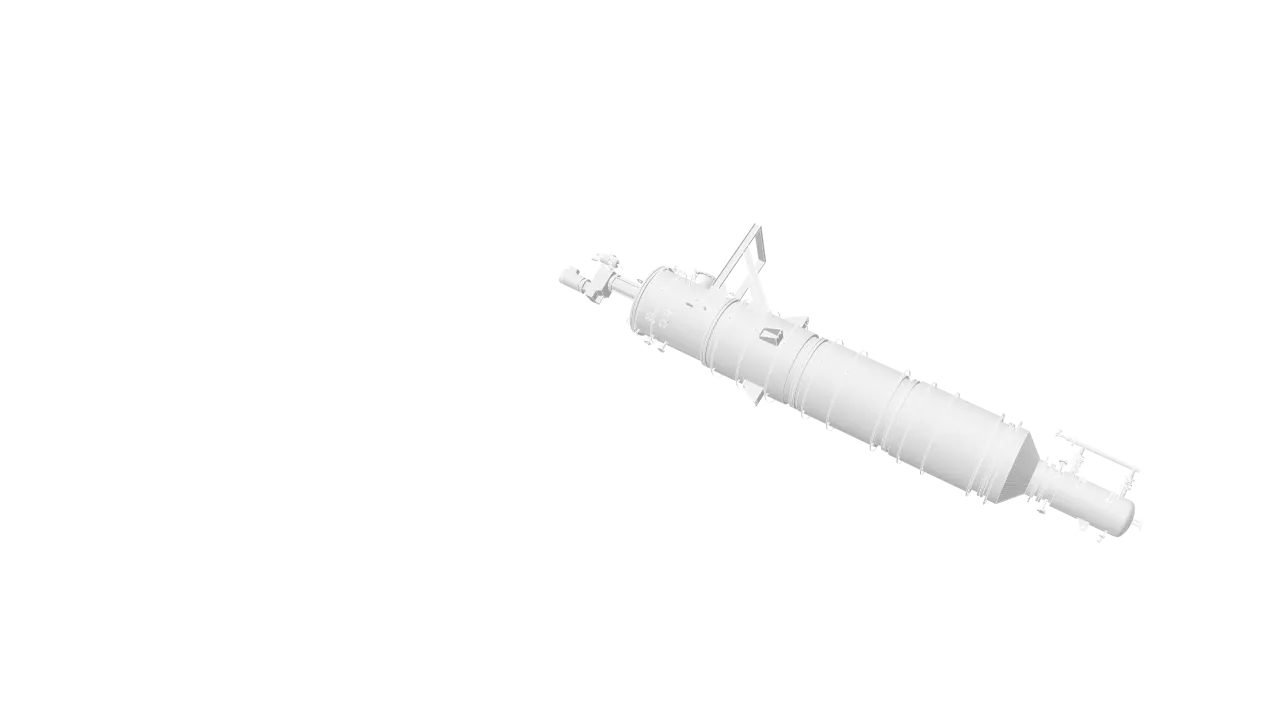
Horizontale Dünnschichtverdampfer
Klassenbester horizontaler Dünnschichtverdampfer
Legierung DestillationVerdampfung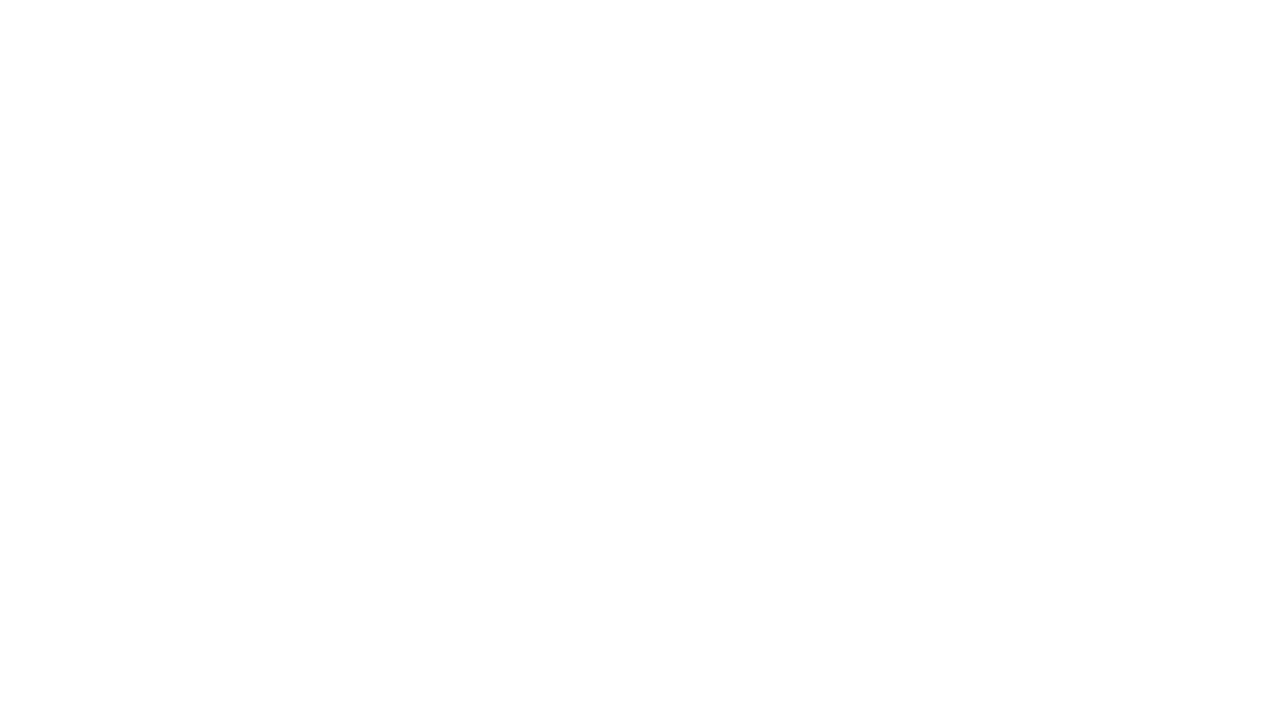
MEMBRANE TECHNOLOGY
De Dietrich Process Systems verwendet diese Technologie zur Trennung von Alkoholen, Lösungsmitteln, Aromen und Gerüchen, die als Gemisch in einem Strom vorhanden sind.
Legierung DestillationVerdampfung