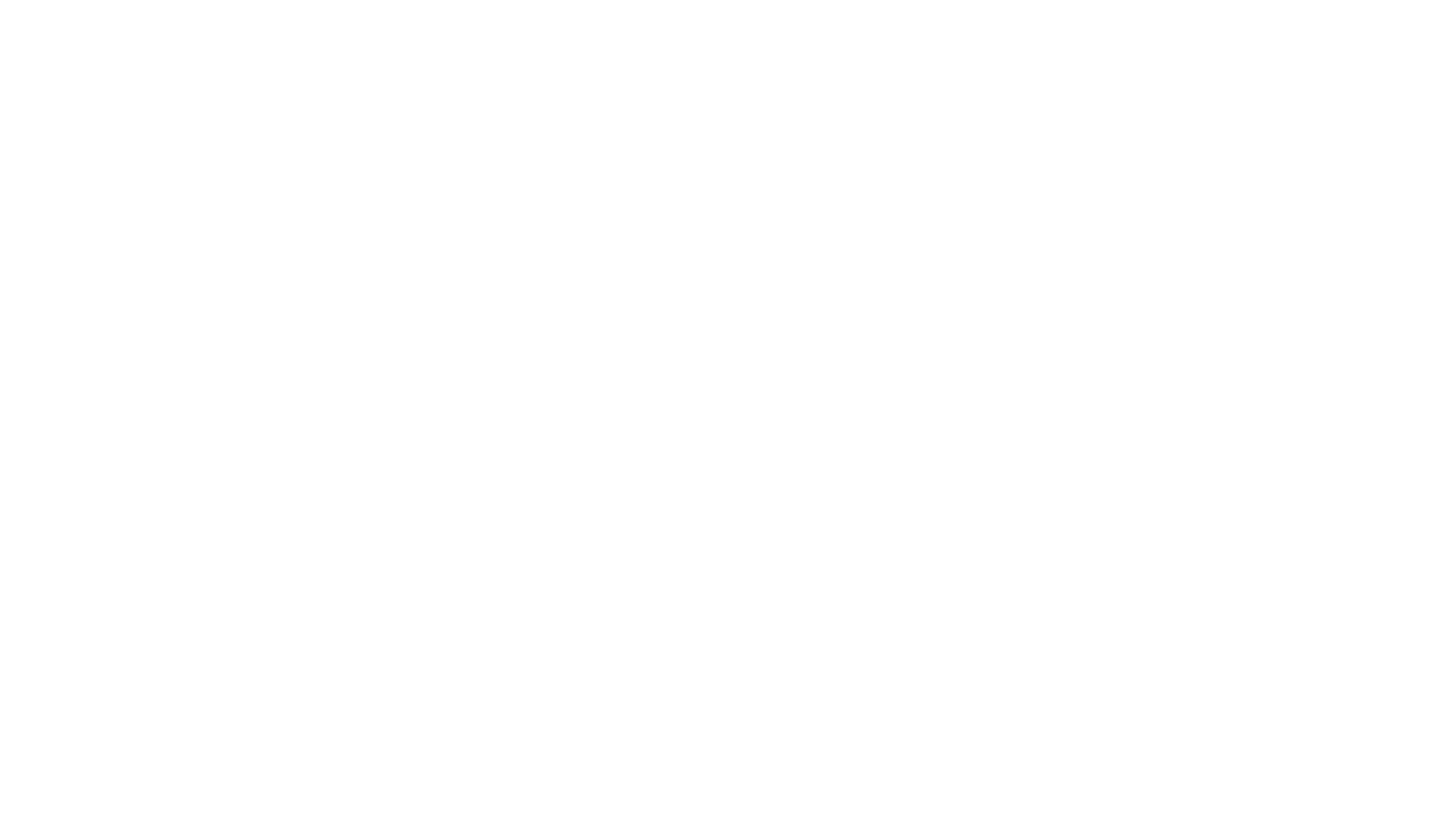
RÉCUPÉRATION DE L’ACIDE ACÉTIQUE CONTENUE DANS LES EAUX USÉES
- Récupération maximale d’acide acétique -
- Élimination maximale d’autres substances organiques -
- Consommation minimale d’énergie -
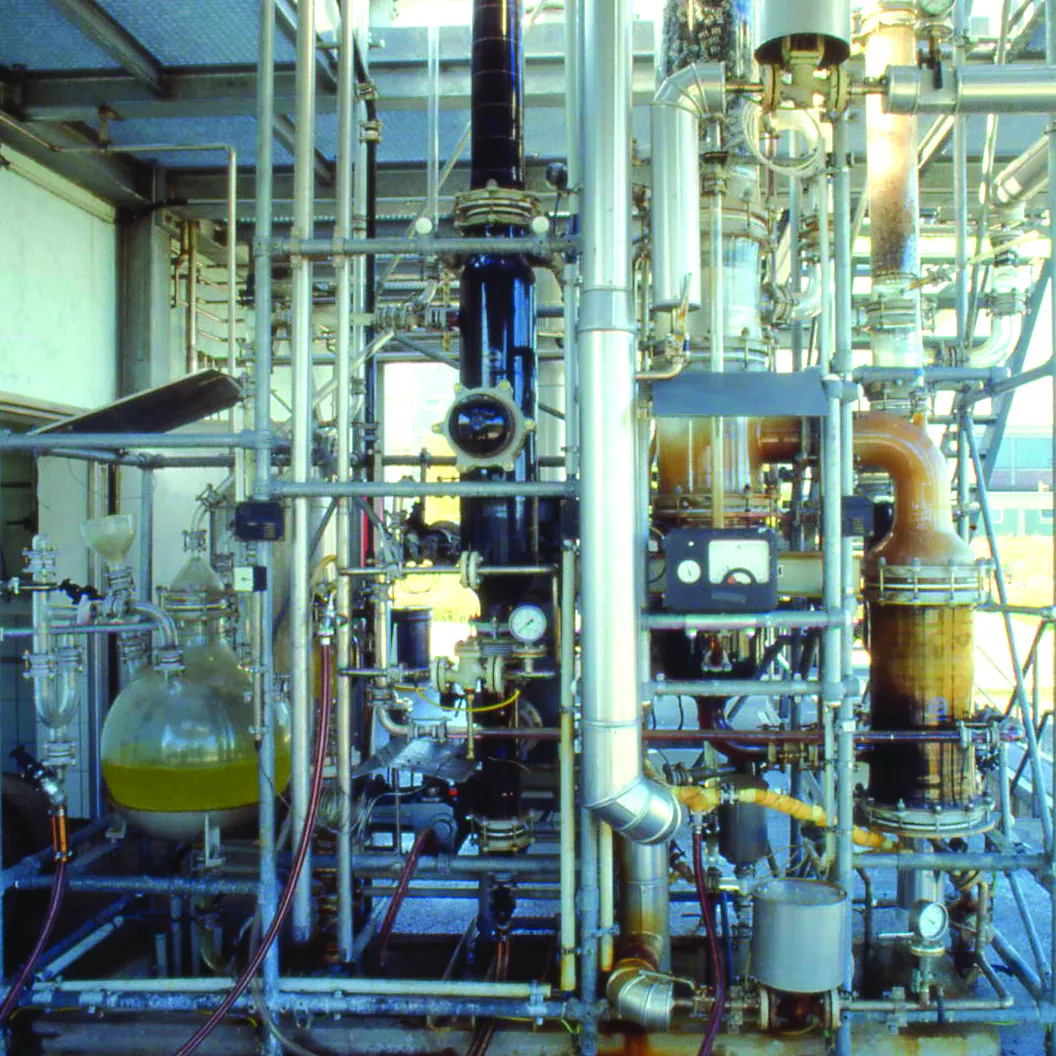
L'acide acétique est l'acide carboxylique aliphatique le plus utilisé. Outre son utilisation comme réactif, par exemple dans la production d'esters d'acide acétique, il est également souvent utilisé comme solvant, par exemple dans la production d'acétate de cellulose ou dans la fabrication de produits pharmaceutiques. Ces processus produisent généralement de l'acide acétique aqueux, dont la récupération revêt dans la plupart des cas une grande importance économique.
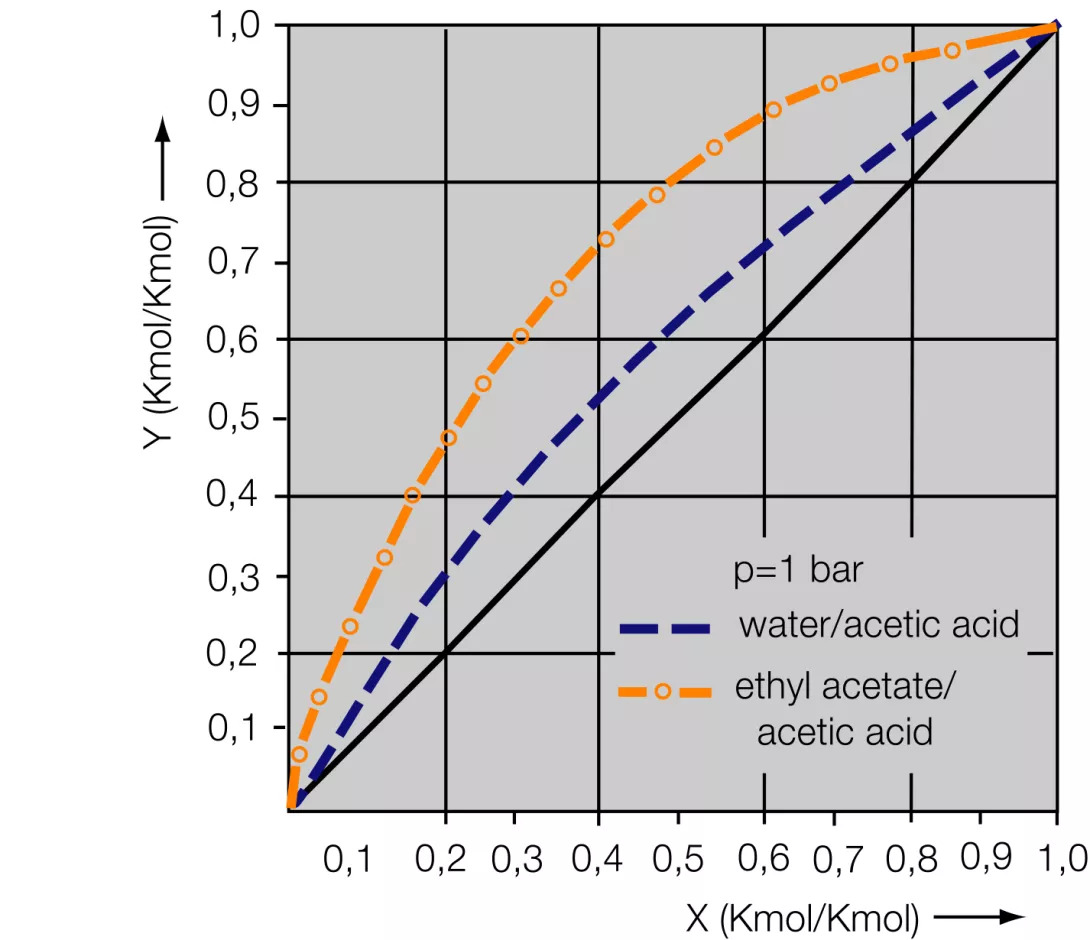
La séparation du mélange acide acétique/eau par simple rectification est ici exclue, car ce mélange présente un très faible facteur de séparation. On aurait alors besoin de colonnes avec un grand nombre d'étages, qui devraient être exploitées avec un rapport de reflux élevé. Dans ce cas, il faut s'attendre à des coûts d'énergie et d'exploitation élevés si l'on n'utilise pas de rectification avec compression des vapeurs. C'est pourquoi la rectification azéotropique s'est imposée dans la pratique, avec ou sans étape d'extraction selon la concentration en acide acétique. L'ajout d'un adjuvant permet d'augmenter la volatilité de l'eau et donc de réaliser la séparation avec une dépense énergétique moindre. Lorsque la concentration en acide acétique est inférieure à 40 % en poids, l'acide acétique est d'abord extrait de la solution aqueuse à l'aide d'un agent d'extraction approprié avant d'être récupéré pur dans la rectification zéotropique. Le procédé de préparation avec extraction doit être envisagé indépendamment de la concentration si des additions supplémentaires dans le mélange de départ, comme par exemple des sels, poseraient des problèmes lors du traitement direct par distillation.
CHOIX DE L'AGENT D'EXTRACTION
Des agents d'extraction à point d'ébullition plus bas sont généralement utilisés. Le choix doit tenir compte de propriétés telles que la solubilité dans l'eau, la capacité d'absorption, le coefficient de partage, le prix, la disponibilité et la composition du point azéotropique, ainsi que des exigences en matière de protection de l'environnement et de la santé. Le tableau 1 présente une sélection d'agents d'extraction appropriés pour la récupération de l'acide acétique, avec des informations sur le coefficient de partage moyen entre la phase organique et la phase aqueuse, la densité de l'agent d'extraction à 20°C, l'enthalpie de vaporisation et la température d'ébullition de l'agent d'extraction, ainsi que la proportion d'eau et la température de l'azéotrope binaire entre l'agent d'extraction et l'eau. Les coefficients de partage moyens ne sont pas très différents. Ainsi, tous les agents d'extraction énumérés ici doivent être considérés comme pratiquement équivalents en termes d'extraction. La rentabilité de l'ensemble du processus dépend fortement des besoins énergétiques de la rectification des solvants, qui dépendent à leur tour du rapport de retour et donc de la puissance du condenseur et de l'évaporateur. La différence de température d'ébullition entre l'acide acétique pur (118°C) et le point azéotropique fournit une indication quantitative de l'importance du rapport de reflux. Par conséquent, le taux de reflux devrait être du même ordre de grandeur pour tous les agents d'extraction énumérés ici. Cependant, la consommation d'énergie dépend également de l'enthalpie de condensation du mélange azéotropique, qui est elle-même déterminée par la teneur en eau de l'azéotrope. Ainsi, la consommation d'énergie devrait être la plus faible lors de l'utilisation d'EtAc ou de MTBE comme agent d'extraction. Il s'avère que ces considérations ne sont valables que jusqu'à certaines concentrations d'entrée de l'acide acétique, qui sont par exemple d'environ 15 % en poids pour l'acétate d'éthyle et le MTBE. Si les concentrations d'entrée sont plus élevées, il faut augmenter la quantité d'agent d'extraction en fonction du bilan et de l'équilibre vapeur-liquide, ce qui augmente les coûts d'exploitation. Le procédé QVF décrit ci-après constitue une alternative plus avantageuse du point de vue énergétique, dans laquelle une gestion appropriée du processus permet d'obtenir un fonctionnement économique de l'ensemble du procédé même en cas de concentrations d'entrée élevées en acide acétique.
Les équilibres liquide/liquide pour les deux systèmes à trois substances préférés (voir figure ci-dessous) montrent que l'utilisation d'acétate d'éthyle entraîne une solubilité mutuelle notable avec l'eau. La surface de l'espace de mélange est relativement petite, de sorte qu'une concentration d'alimentation de 30 % en poids ne doit pas être dépassée pour un fonctionnement sûr de l'extraction. En revanche, l'écart de mélange est plus marqué dans le système MTBE / acide acétique / eau et la solubilité mutuelle est plus faible. Les mélanges d'alimentation avec des concentrations d'acide acétique jusqu'à environ 40 % en poids peuvent donc être traités sans problème avec du MTBE comme agent d'extraction.
Fig. à droite Diagramme d'équilibre du système MTBE / acide acétique / eau
(données en % en poids à 20°C) et Fig. à gauche Diagramme d'équilibre du système acétate d'éthyle / acide acétique / eau (données en % en poids à 20°C)
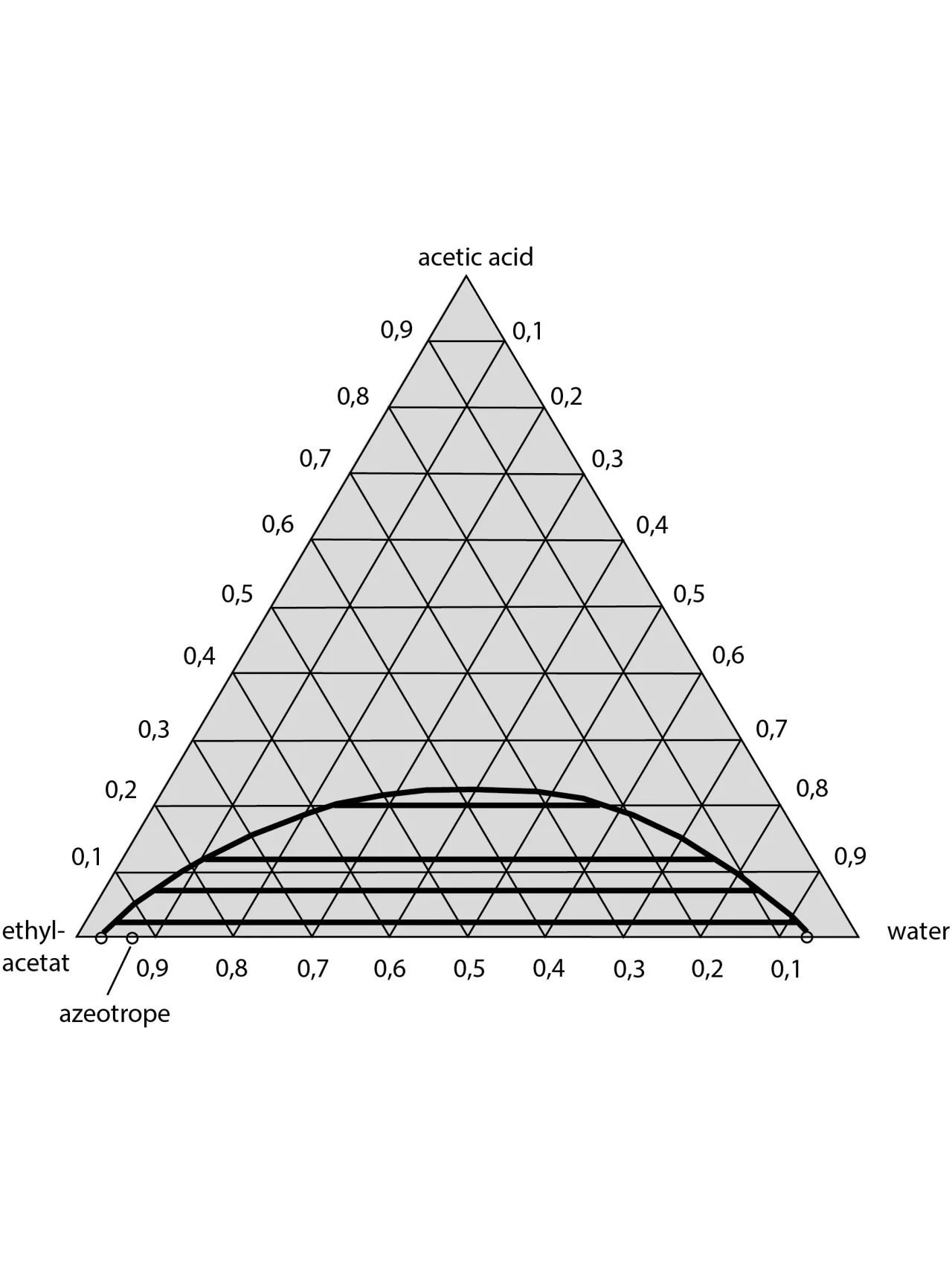
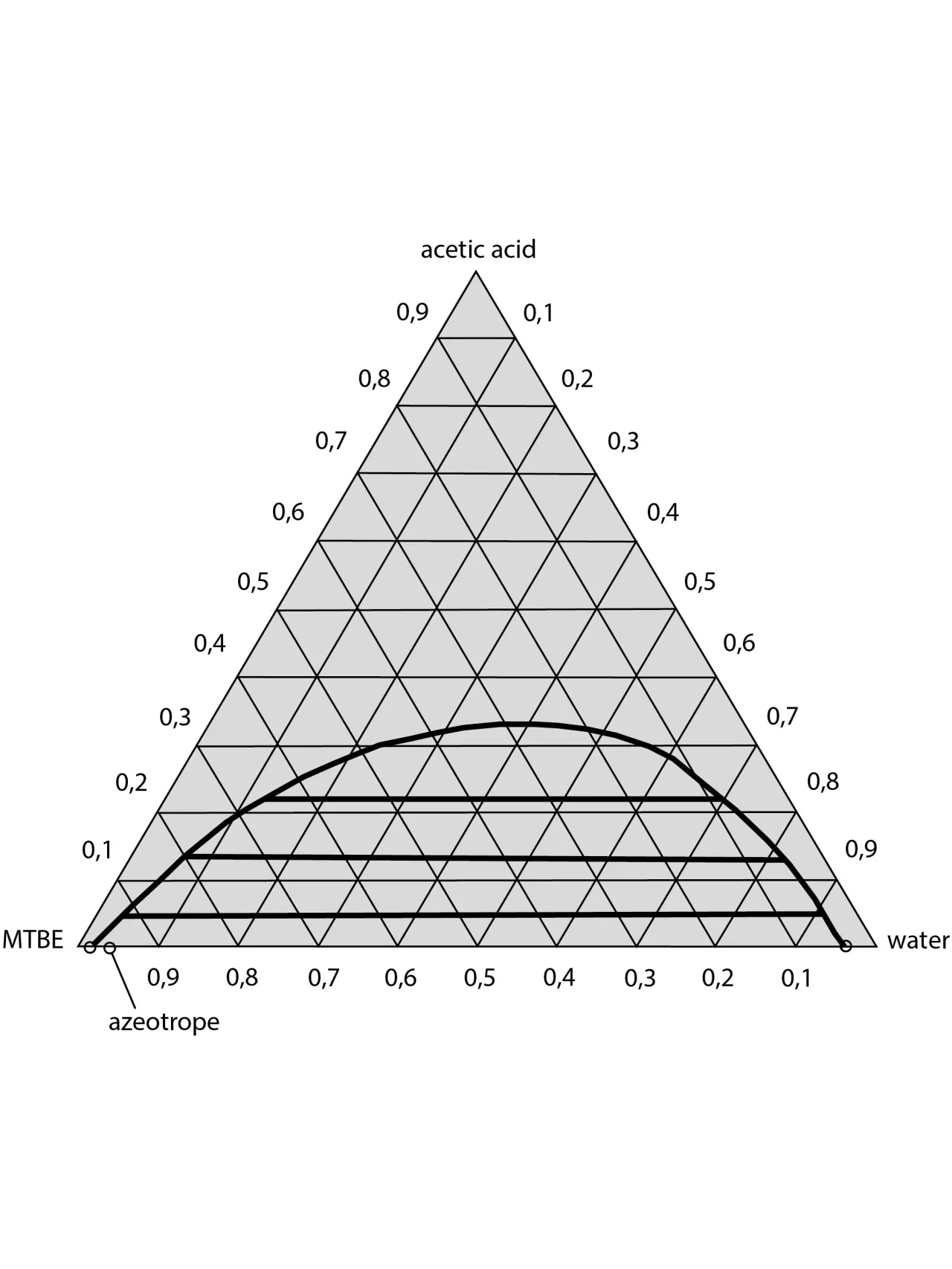
Name | Average distribution coefficient | Density | Enthalpy of vaporisation | Boiling Point | Azeotrope |
kg/kg | kg/m³ | kJ/kg | °C | Water T Wt % °C | |
Ethyl acetate C4H8O2 | 0,84 | 900 | 395 | 76,7 | 8,47 70,4 |
Isopropyl acetate, C5H10O2 | 0,55 | 877 | 361 | 88,6 | 10,50 76,5 |
n-Propyl acetate, C5H10O2 | 0,50 | 891 | 336 | 101,6 | 13,20 82,2 |
Methylpropyl ketone, 2-pentanon, C5H10O | 0,97 | 810 | 384 | 102,3 | 19,50 83,3 |
Methylisobutylketon, 4 Methyl- 2-Pentanon C6H12O | 0,50 | 810 | 488 | 115,9 | 24,30 87,9 |
Methyl-tert.-butyl ether, C5H12O | 0,75 | 740 | 322 | 55 | 4 52,6 |
PROCESSUS D'EXTRACTION
La figure ci-dessous montre le schéma d'une installation d'extraction classique pour la récupération de l'acide acétique. Elle se compose d'une colonne d'extraction, d'une colonne de rectification pour la récupération du solvant d'extraction et d'une colonne de stripage à l'eau. Le mélange entrant présente généralement une densité supérieure à celle du solvant et est introduit en tête de la colonne d'extraction. Il s'écoule vers le fond de la colonne et libère ainsi l'acide acétique dans l'agent d'extraction, ce qui permet d'atteindre des concentrations résiduelles de 0,1 à 0,5 % en poids, selon la charge de travail. Comme la phase aqueuse se sature en même temps que l'agent d'extraction dans la colonne d'extraction, celle-ci est récupérée dans une colonne de stripage placée en aval. Il est alors possible de travailler avec de la vapeur directe. Dans la colonne de rectification, l'agent d'extraction se dépose en tête et l'acide acétique en fond de colonne, des concentrations pouvant être réglées jusqu'à près de 100 % en poids d'acide acétique. S'il existe un risque que des composants à point d'ébullition plus élevé passent dans la phase organique lors de l'extraction, il est recommandé d'extraire l'acide acétique sous forme de vapeur. La figure en bas à droite montre le schéma d'écoulement du procédé QVF. Comme dans le procédé traditionnel, l'acide acétique est extrait de l'eau de traitement dans l'étape d'extraction à l'aide d'un agent d'extraction approprié (dans la plupart des cas, du MTBE). La colonne d'extraction est toutefois exploitée de manière à obtenir une concentration aussi élevée que possible d'acide acétique dans la phase d'extrait en cours, tout en respectant la pureté du raffinat requise. Avec ce mode de fonctionnement, la phase d'extraction contient une forte proportion d'acide acétique et, par conséquent, d'eau. Dans l'étape de rectification en aval, on procède à la séparation de la phase d'extrait en un azéotrope d'agent d'extraction et d'eau, ainsi qu'en acide acétique de la concentration souhaitée. L'eau présente en excès dans la phase d'extrait est retirée sous forme de courant latéral liquide dans la partie d'amplification de la colonne de rectification. Un choix particulièrement avantageux du point de soutirage et du rapport de reflux permet de régler une composition dans le courant latéral qui correspond à peu près à celle de l'eau de traitement. Après avoir été refroidi à la température de fonctionnement de l'étape d'extraction, le flux latéral est réintroduit dans la colonne d'extraction. L'emplacement du point d'alimentation dépend de la concentration d'acide acétique dans le flux latéral. Le coût de l'ensemble du processus est déterminé par le coût de la séparation de l'agent d'extraction de l'acide acétique. Tant le dimensionnement que la conception de la régulation de cette étape du processus doivent donc être effectués avec soin. Dans le cas du procédé classique avec l'acétate d'éthyle ou le MTBE comme agent d'extraction, la séparation peut être réalisée sans problème. Il faut toutefois veiller à ce que le rapport entre l'acétate d'éthyle et l'eau dans la colonne soit tel que le facteur de séparation soit le plus élevé par rapport à l'acide acétique. Cela est très facile à réaliser si la concentration d'acide acétique d'alimentation dans l'eau de traitement est inférieure à 15 % en poids.
L'étape de rectification ne pose pas non plus de problème dans le procédé QVF. Cependant, la régulation de la colonne est plus complexe par rapport au procédé traditionnel. Ainsi, il faut régler dans la colonne un profil de concentration déterminé avec un maximum de concentration prononcé pour l'eau. De plus, le débit du flux latéral doit être régulé. Le concept de régulation QVF® développé par De Deitrich Process Systems à cet effet a fait ses preuves dans la pratique.
Fig. à gauche : schéma du procédé classique et fig. à droite : schéma du procédé QVF.
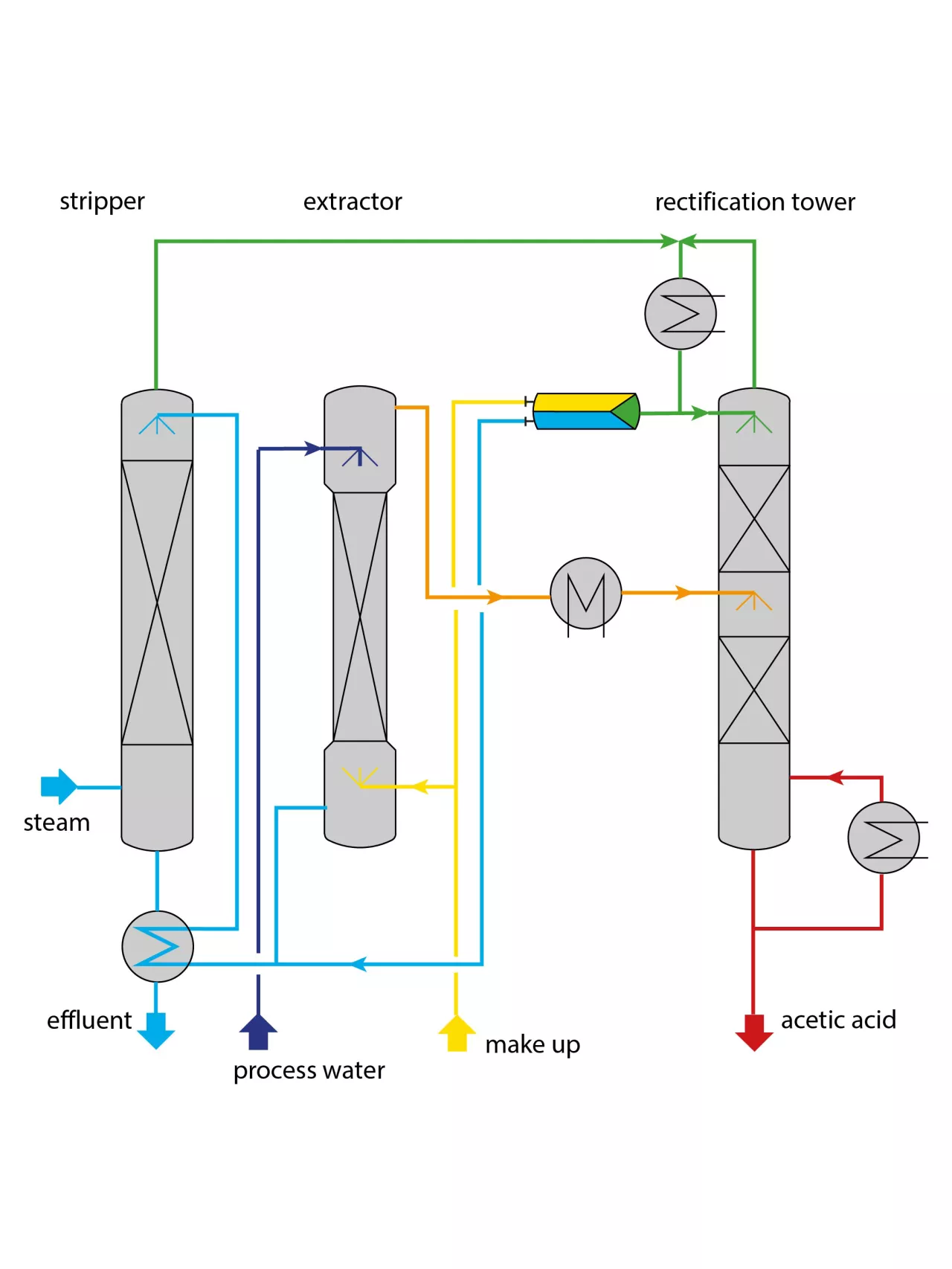
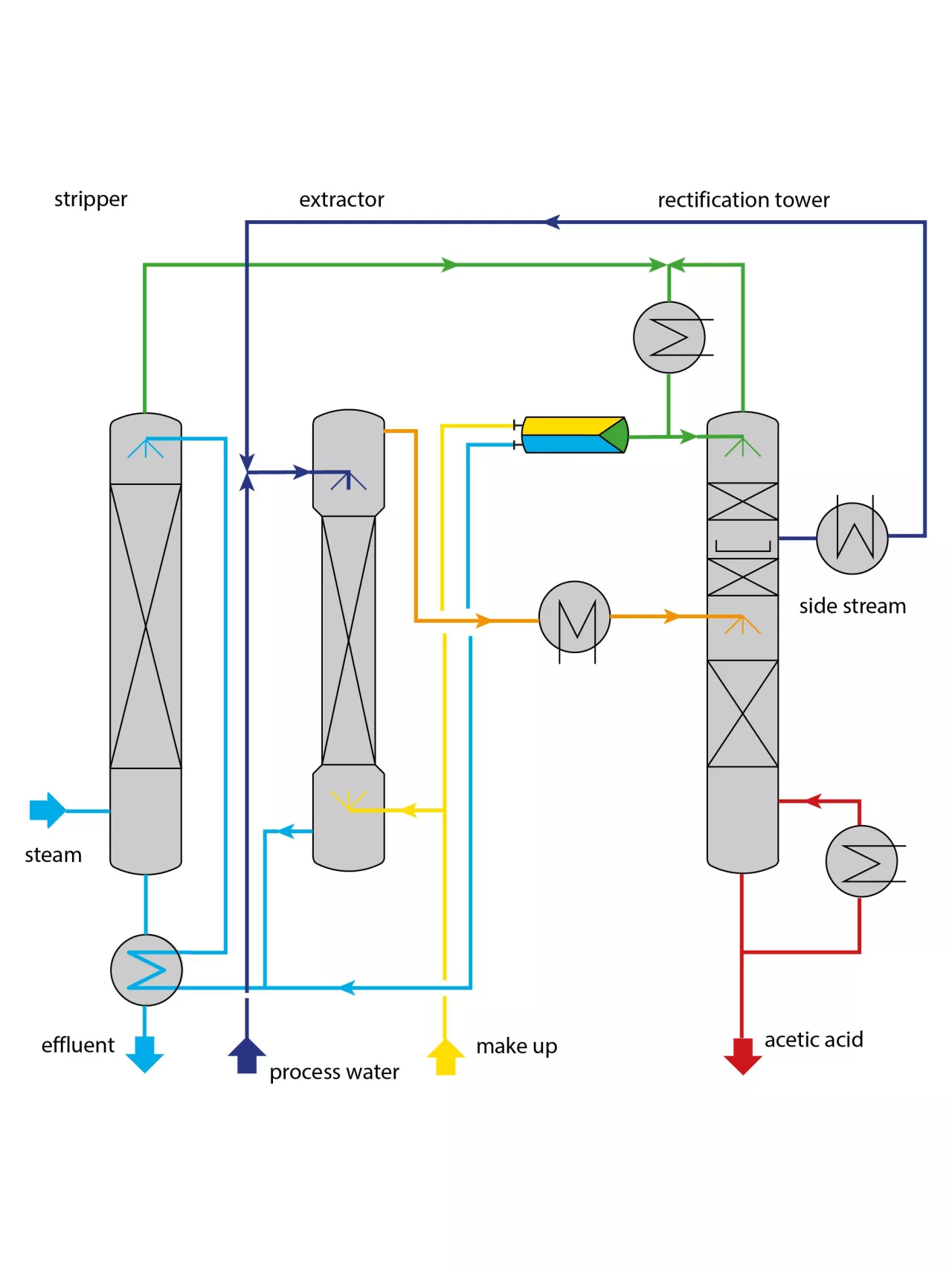
FRAIS D’EXPLOITATION
La mise en œuvre plus compliquée du procédé QVF® se justifie par une diminution du besoin en énergie allant jusqu’à 40 % en comparaison du procédé traditionnel. C’est la réduction du flux d’agent d’extraction qui est en premier lieu à l’origine de cette économie. Ceci a pour conséquence d’importantes concentrations en acide acétique dans l’extrait en sorte que la proportion en eau de l’extrait est plus importante que dans le procédé classique. Mais l’excédent d’eau est évacué de la colonne de rectification sous forme liquide par une ouverture latérale. De cette façon, l’obtention d’un mélange azéotrope dans le distillat est rendue possible, à quoi il faut ajouter que seule la quantité d’eau qu’il contient doit être condensée en tête de colonne.
D’une manière générale, il n’est pas possible de chiffrer précisément les coûts liés à la récupération de l’acide acétique étant donné qu’ils dépendent de la concentration d’arrivée de l’acide acétique, de la concentration des produits en sortie, de la nature de l’agent d’extraction, du choix du procédé, de la récupération de la chaleur, etc. Deux valeurs de référence permettant une évaluation des coûts sont indiquées ci-après pour chacun des procédés. Les chiffres donnés valent pour l’utilisation du MTBE et dans l’hypothèse où un acide acétique d’une concentration de 99 % pds, liquide et en ébullition, est extrait en pied de colonne de rectification.
Avec le procédé classique, la puissance de l’appareil à évaporer est
- d’environ 280 kW par 100 kg/h d’acide acétique en présence d’une concentration d’entrée de 10 % pds en acide acétique,
- d’environ 260 kW par 100 kg/h d’acide acétique en présence d’une concentration d’entrée de 35 % pds en acide acétique,
Avec le procédé QVR® les valeurs suivantes sont obtenues :
- environ 260 kW par 100 kg/h d’acide acétique en présence d’une concentration d’entrée de 10 % pds en acide acétique,
- environ 180 kW par 100 kg/h d’acide acétique en présence d’une concentration d’entrée de 35 % pds en acide acétique.
L'ÉTIQUETAGE DES ÉLÉMENTS D'ACCOMPAGNEMENT
Dans de nombreux cas, l'eau de traitement contient des composants à faible point d'ébullition comme l'éthanol ou l'acétone, qui doivent être éliminés en même temps que l'acide acétique. En utilisant le MTBE comme agent d'extraction, on peut procéder comme suit. En régime permanent, les composants à bas point d'ébullition passent par la tour d'extraction sans être extraits et atteignent un stripper en aval, qui est équipé d'une section de rectification (voir figure).
Dans la section de stripage de la tour, l'eau est débarrassée de l'agent d'extraction et des composants qui l'accompagnent. D'autre part, la section de rectification de la tour est utilisée pour séparer le MTBE des composants qui l'accompagnent. Cependant, lors de la séparation des composants dont la différence de température d'ébullition avec le MTBE est faible (par exemple l'acétone), on peut s'attendre à des pertes de MTBE. Dans ce cas, il est possible de recourir à une autre variante du procédé. Pour ce faire, on utilise un stripper à eau sans section de rectification. Toutefois, le stripper est exploité de manière à ce que les composants d'accompagnement soient dirigés vers le bas de la tour et l'agent d'extraction vers le haut de la tour. Dans ce cas, il est toutefois nécessaire de purifier la phase aqueuse chargée, par exemple par un traitement biologique.
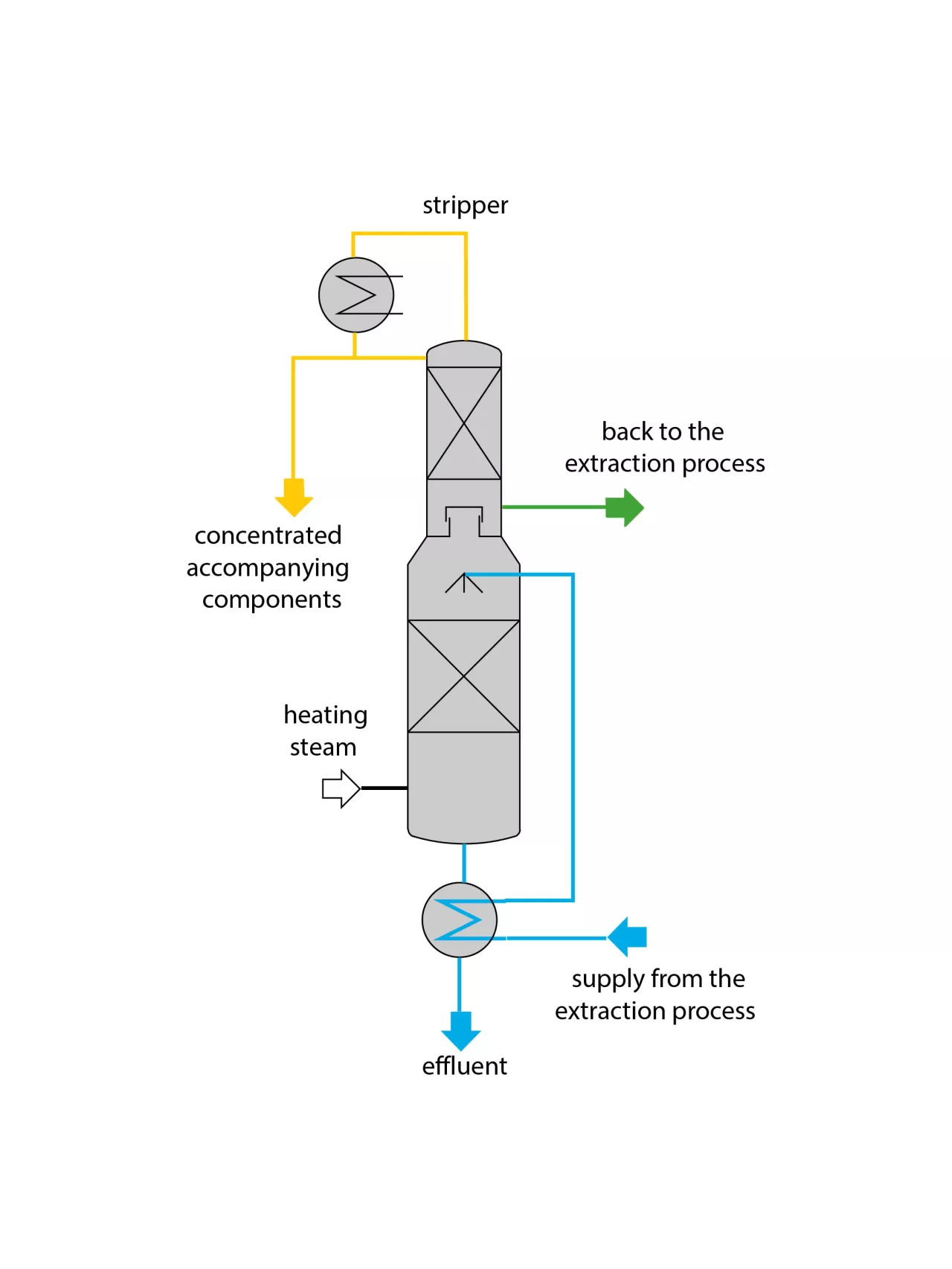
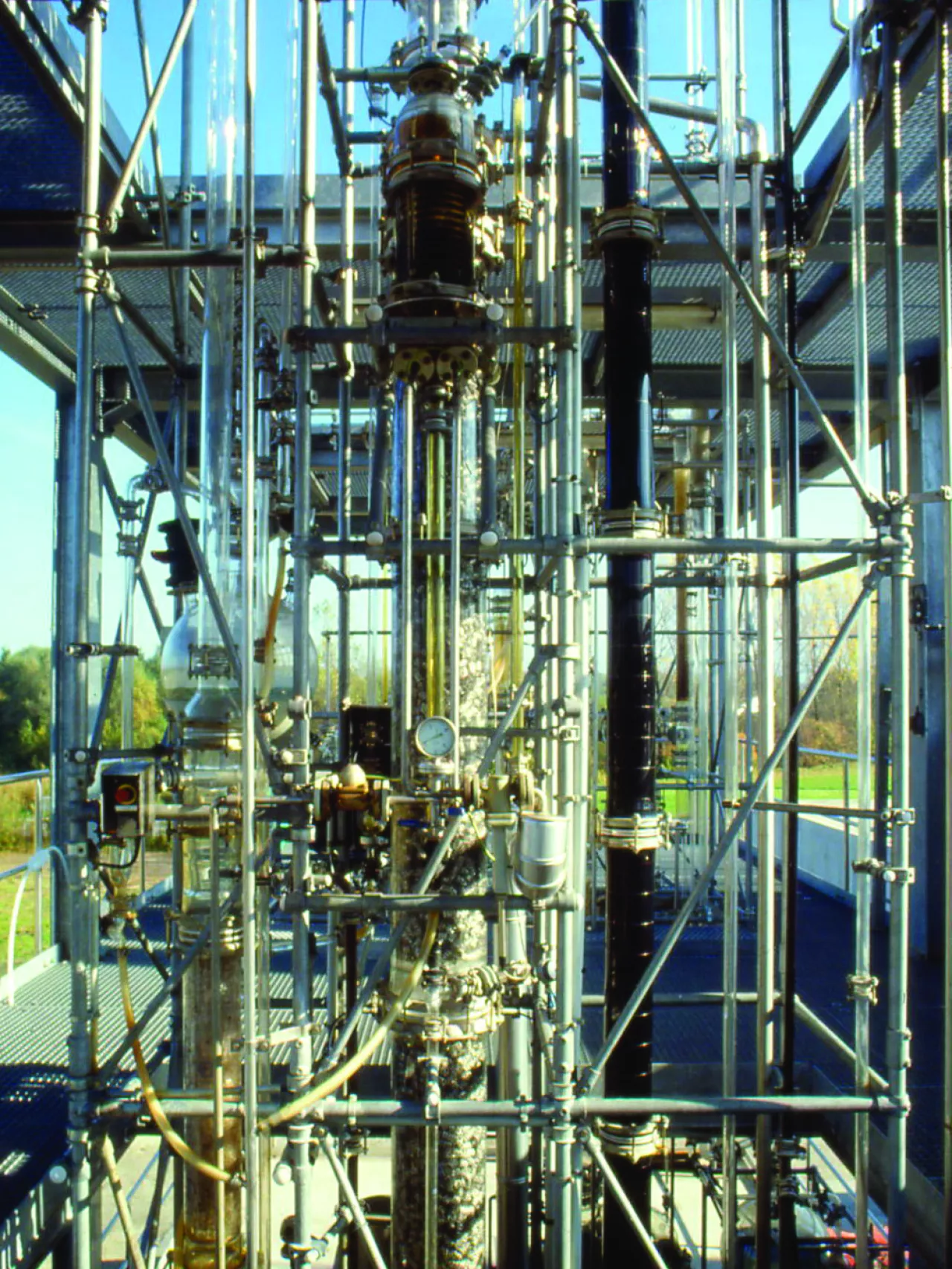
Vous avez des questions ?
Nos équipes sont prêtes à collaborer avec vous et à fournir des solutions pour vos projets
Documents à télécharger
Demande de téléchargement
Afin de traiter efficacement votre demande de brochure, nous vous demandons de bien vouloir fournir les informations requises à l'aide de notre formulaire.