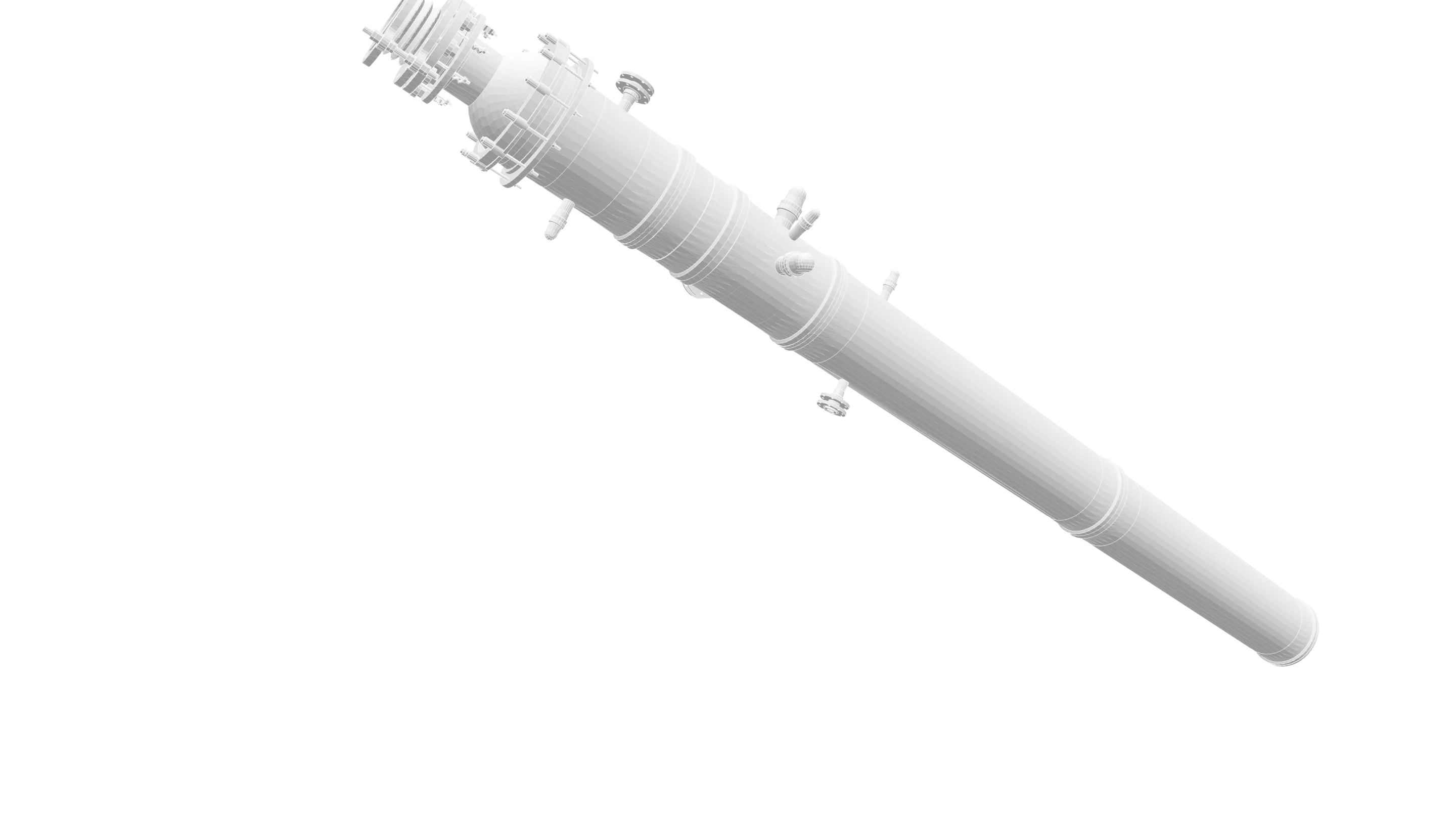
COLONNES D'EXTRACTION
Séparation de produit en continu
Réalisation rentable de processus à étages multiples
Divers types de design adaptés à différentes applications
La solution rentable pour des processus d'extraction à étages multiples
Solution rentable pour des processus d'extraction à étages multiples
Plus le nombre d'étages de séparation théoriques à réaliser augmente, plus les colonnes d'extraction deviennent intéressantes économiquement, comparées aux mélangeurs-stabilisateurs. En effet, l'élévation du nombre d'étages de séparation théoriques accroît simplement la hauteur de la colonne. Les 2 phases liquides traversent la colonne par gravité à contre-courant. Dans les colonnes d'extraction, les mêmes 2 étapes de processus de mélange et de stabilisation doivent être assurées par un étage de séparation.
Le processus de mélange dans une colonne peut être assuré de diverses manières différenciées par les types de colonne d'extraction.
Le processus de stabilisation dans les colonnes est surtout moins efficient que dans les mélangeurs-stabilisateurs. En effet, le mélange et l'entraînement de dispersion sont plus inévitables et plus ou moins fixes suite à la sélection du processus de mélange et donc du type de colonne d'extraction.
De Dietrich Process Systems offre différents types de colonne, notamment :
De ce fait, le type de colonne doit être sélectionné avec le plus grand soin selon la spécificité du processus d'extraction. C'est essentiellement le fruit de l'expérience concrète d'un processus donné d'extraction ou d'essais qui peuvent être effectués dans notre hall expérimental. |
COLONNES D'EXTRACTION PULSÉES
Comme le nom l'indique, l'énergie de dispersion est introduite dans cette colonne avec un pulsateur. Nous fournissons des colonnes pulsées DN50 à DN600 en verre borosilicaté 3.3 comme matériau de prédilection. L'ensemble du liquide des deux phases contenu dans la colonne est pulsé ver le haut et le bas. Le flux dans les éléments internes, ainsi les cribles ou le garnissage, génère le processus de mélange.
Colonnes à garnissage
Des garnissages aussi bien aléatoires que structurés sont employés. Par cohérence avec la résistance à la corrosion de nos colonnes en verre borosilicaté 3.3, nous préférons les anneaux de Raschig de différentes tailles et notre garnissage structuré exclusif DURAPACK® - tous deux en verre borosilicaté glass 3.3. Les colonnes à garnissage sont dépourvues de zones de colonne de stabilisation distinctes. Elles sont donc plus favorables pour les processus de séparation à phase rapide tout en impliquant des coûts d'investissement relativement bas. À nouveau, il est préférable de fonder la sélection du bon garnissage sur les essais pour un processus donné.
Colonnes à plateaux à crible
Contrairement aux colonnes à garnissage, les zones de stabilisation dans les colonnes à plateaux à crible peuvent être agrandies en espaçant les cribles. Les cribles sont fixés sur un arbre central avec un espacement minimum ou étanche par rapport à la paroi intérieure en verre de la colonne. Pour les colonnes à plateaux à crible, non seulement peut-on varier la distance des plateaux mais aussi la zone à section libre de 7 à 50%. L'acier inox est le matériau de fabrication le plus économique si aucun problème de corrosion n'est envisagé. Sinon, les plateaux à crible peuvent aussi être exécutés en verre borosilicaté 3.3 et en PTFE.
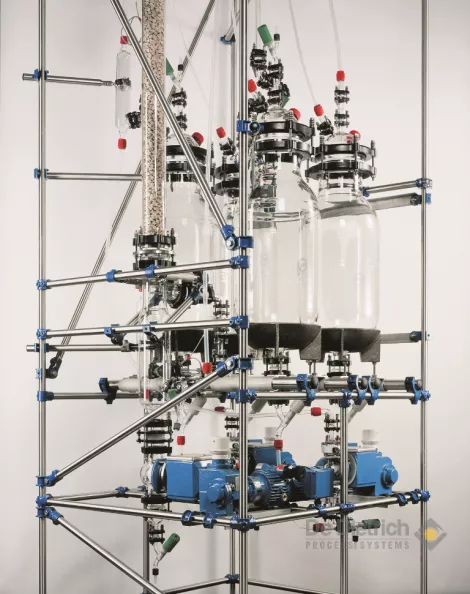
COLONNES KARR Pour les colonnes d'extraction pulsées, le liquide contenu est pulsé vers le haut et le bas. Pour une colonne de type KARR, c'est l'arbre central avec les cribles qui oscille. La longueur et la fréquence de ce mouvement sont adaptables au processus avec nos colonnes de type KARR disponibles jusqu'à DN600. Les cribles présentent normalement une grande zone de section libre de 50% et l'espacement à la paroi est supérieur à celui des colonnes à plateaux à crible du fait du mouvement. En combinaison avec le démantèlement relativement facile de l'arbre, ce type de colonne est privilégié dès lors que des solides sont présents dans le processus. | |
CONTACTEUR À DISQUE ROTATIF - CDR Pour une colonne CDR, l'arbre central reçoit des disques fixes rotatifs. En outre, des bagues annulaires dénommées stators sont placées à l'intérieur de la colonne, toujours à mi-distance entre deux disques. Ces stators sont soit en métal et insérés dans la colonne, soit en verre borosilicaté et intégrés dans la colonne. Les disques présentent un diamètre inférieur au diamètre intérieur des stators de sorte à faciliter le démantèlement de l'arbre. Diamètres et distances sont à adapter au processus. En fonctionnement, seule le régime de rotation est modifiable, outre le débit. |
EXTRACTION À AGITATION DE CELLULES - EAC La colonne EAC QVF® a été développée par De Dietrich Process Systems. Comme dans une colonne EAC, un arbre central tourne et des stators sont installés dans la colonne. Au lieu de disques, de véritables agitateurs sont fixés sur l'arbre alors que les stators reçoivent des déversoirs à encoche sur leur bord intérieur. Les agitateurs affichent une efficience de mélange plus élevée que les disques et le déversoir à encoche améliore la phase de séparation en agrandissant la plage de débit. L'arbre d'agitateur et les stators sont combinés dans des modules uniques en acier inox ou d'autres métaux. La jonction de ces modules assure la longueur active requise dans la colonne d'extraction en verre borosilicaté 3.3. COMMENT IDENTIFIER LA MEILLEURE SOLUTION ? Outre les calculs théoriques et l'expertise en extraction accumulés au fil de son histoire, De Dietrich Process Systems se fait un plaisir de mener à bien des essais dans notre hall expérimental afin de développer un processus optimum et de sélectionner l'équipement d'extraction le plus adapté à vos spécificités. Le verre borosilicaté 3.3 est un matériau idéal pour un équipement d'extraction car le processus peut être optimisé tout en l'observant visuellement avec facilité. |
Demande de téléchargement
Afin de traiter efficacement votre demande de brochure, nous vous demandons de bien vouloir fournir les informations requises à l'aide de notre formulaire.