The cheat sheet for GlasLock® Blades
The GlasLock® interchangeable blade system is the agitator of choice for many of processes
that utilize glass-lined steel equipment
The GlasLock® system can be adjusted, removed and interchanged, a quality that is especially important in processes that can undergo so many changes. Unlike a one-piece agitator which is selected based on specific process objectives, GlasLock® blades can be set to various angles or swapped out for different shaped blades to accomplish different mixing objectives.
BENEFITS OF REMOVABLE BLADES
- Reduce maintenance downtime and cost
- Maximize process flexibility
- Improve product yield and quality
- Reduce batch time and cost
- Fit the agitator to your process, not your process to the agitator
- Improve heat transfer efficiency by up to 30%
- Be replaced or adjusted to a new blade design or pitch to suit process needs
- Be individually replaced when they are damaged, not the entire agitator, without disturbing the mechanical seal
- Be installed with easy-to-use tools, with no hazardous cryogenic fluids to handle
These benefits combine efficiency, productivity, and convenience to create an optimized mixing solution.
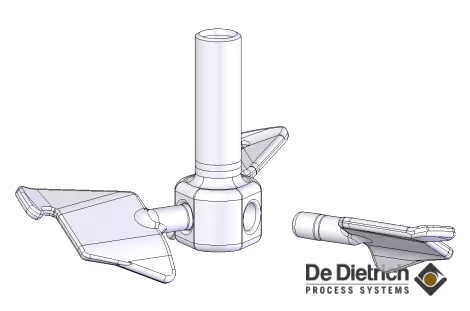
OPTIFOIL ADVANTAGES
OptiFoil’s hybrid design ensures a high axial flow for suspension processes and facilitates the operation of minimum volumes. The pitch angle of these blades gives a smoother contact with the product than the vertical trapezoidal blades and is specifically recommended to avoid the alteration of fragile crystals.
OptiFoil is ideally suited for reactors involving homogenization and suspension, as well as heat transfer, crystallization, and dispersion. Its axial/radial flow is advisable for virtually every process. OptiFoil will also mix higher viscosity liquids than standard flat blades.
FUNCTIONALITY AT EVERY ANGLE AND DESIGN
With a single agitator adapted for each requirement, the GlasLock® system meets the mixing needs of virtually every application.
Pitch blade turbine impellers are the most commonly used type of GlasLock® blades. For general use, including homogenization and heat transfer, they are typically set at a 45 or 60-degree angle.
If your process involves more fragile material, the blades can be set at 30 degrees to effectively and gently handle suspension and crystallization.
For applications involving gas dispersion, absorption, or any kind of gas-liquid reaction, a more turbulent flow can be achieved by setting the blade angle to 90 degrees
The GlasLock® blades are available in a variety of other styles to suit diverse process needs.
Blade designs include:
- Hydrofoil: This profile improves on the pumping effect given by the standard pitch blade turbine impellers. The bends and twists of its construction are specifically adapted to crystallization and suspension processes
- Rushton Turbine: Like a standard blade installed at 90 degrees, the radial flow of a Rushton turbine blade is ideal for applications involving gas dispersion, absorption, and gas-liquid reaction
- Trapezoidal Blade: Specially designed to mix very low product volumes and facilitate the final emptying of the reactor by reducing the gap between the blades and the bottom of the reactor
- Breaker Bars: Multipurpose for heat transfer, homogenization, crystallization and viscous products
- ViscoFoil: Intended for high viscosity
- OptiFoil: Combines the advantages of HydroFoil blades and Trapezoidal blades for optimized mixing
OPTIFOIL ADVANTAGES
OptiFoil’s hybrid design ensures a high axial flow for suspension processes and facilitates the operation of minimum volumes. The pitch angle of these blades gives a smoother contact with the product than the vertical trapezoidal blades and is specifically recommended to avoid the alteration of fragile crystals.
OptiFoil is ideally suited for reactors involving homogenization and suspension, as well as heat transfer, crystallization, and dispersion. Its axial/radial flow is advisable for virtually every process. OptiFoil will also mix higher viscosity liquids than standard flat blades.
THE GLASLOCK® SYSTEM - BASIC SELECTION TABLE
The GlasLock® System provides a lot of choices, with an option to fit nearly every mixing application. Download the brochure with the selection criteria
Other considerations to take into account when selecting the blade design and configuration for your agitator:
- Dual Tiers: GlasLock® agitators with a dual set of blades improve the agitation efficiency in large-size vessels
- Multi-stage mixing: GlasLock® blades are extremely beneficial in multi-stage agitators, as the angle and/or profiles of the blades can be different on each tier, providing exceptional mixing performance.
- Dispersion of Gas: The combination of gas introduction via dip pipe and 60° blades provides exceptional gas dispersion
De Dietrich Process Systems’ team of mixing experts can help you determine the best components to meet your process objectives and we’d be happy to help you spec a reactor to fit the needs of your business.
In addition to GlasLock® blades, De Dietrich Process Systems offers other enhancements that can optimize
the performance of your reactor.