Agitated Nutsche Filter / Dryer
The Nutsche Filter / Dryer (ANFD) and Filter meet the stringent requirements of the pharmaceutical and fine chemicals industries for solids washing, separation & drying.
Tailored to your needs
From the smallest to the largest, from the most simple to the extremely complex Filter / Dryer.
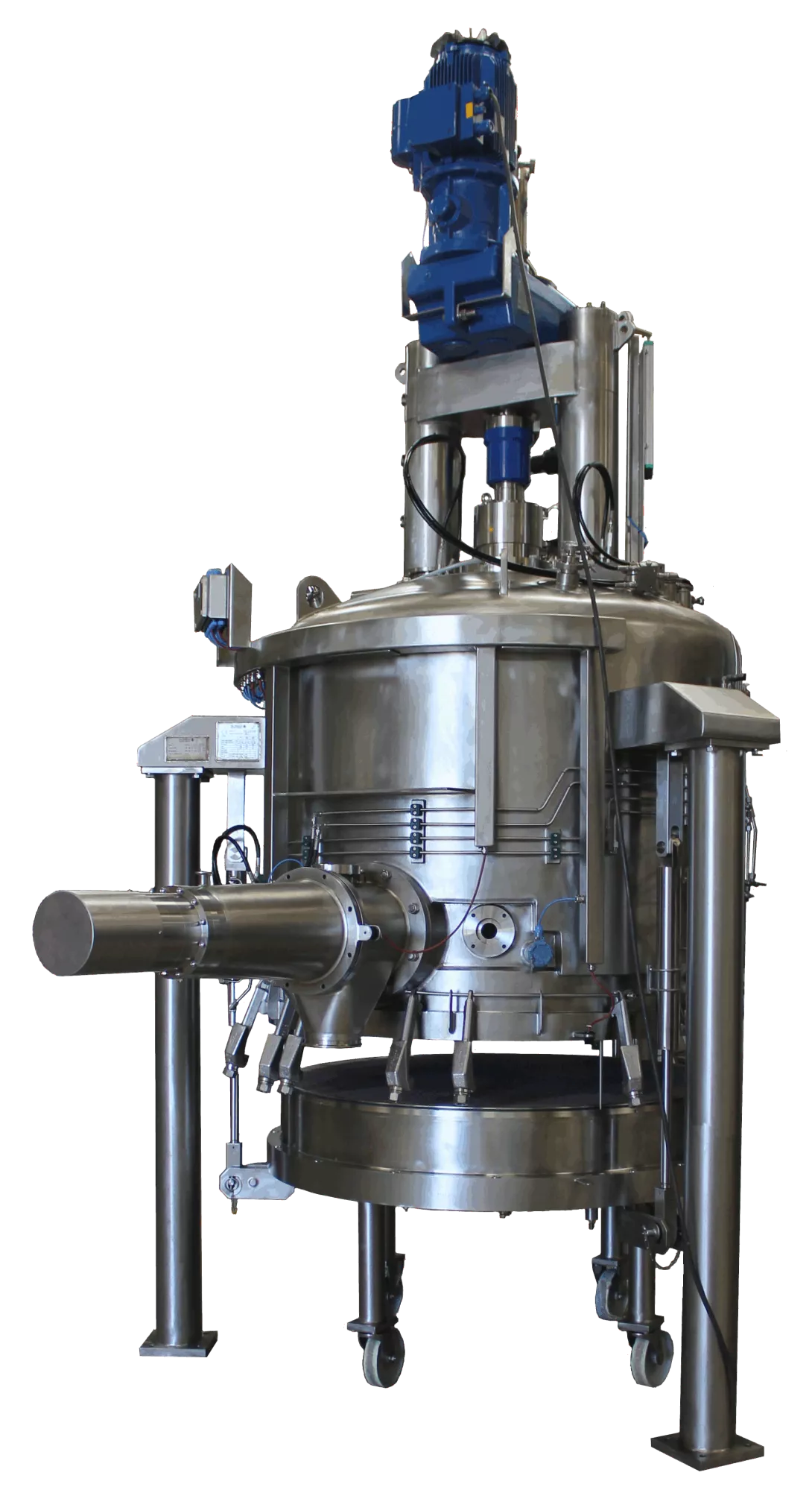
Agitated Nutsche Filter / Dryers are all-in-one solution for liquid-solid separation and powder drying.
The full operation to produce high quality chemicals in solid form occurs in just one equipment. This limits manipulation, preserves your product and make automation easy.
The Filter / Dryer performs a multitude of tasks including filtration, displacement or reslurry washing, vacuum or convection drying.
It can discharge wet cake, slurry, liquid, or dried cake to less than 0.1% moisture.
Filter / Dryers have numerous advantages :
- Limited overall dimensions
- Reduced investment
- Improved product quality
- Closed system : no operator contact, no product transfer from one machine to another.
Key figures of the Filter / Dryers
Benefits of the Nutsche Filter / Dryer
The Filter / Dryer range is based on the famous know-how of Rosenmund, Guedu and Comber to provide the reliable and efficient equipment for chemical or pharmaceutical production.
All-in-one solution for powder separation and drying
High efficiency drying
Ideal for sensitive products
Low risk of contamination and cross-contamination
Industry-Leading Filters & Dryers
Universal Filter Media
The filter plate design allows the use of all types of filter media: cloth, single later metal screen, or multi-layer sintered metal.
Side Discharge Valve
The valve provides a pressure/vacuum-tight seal and eliminates any cleanability issues.
Heated Filter Plate
The underside of the filter plate is designed to optimize drainage during filtration and effectively transfer heat to the cake during drying.
Full discharge
The full discharge of the Filter / Dryer can be manually or automatically operated thanks to unique proprietary options.
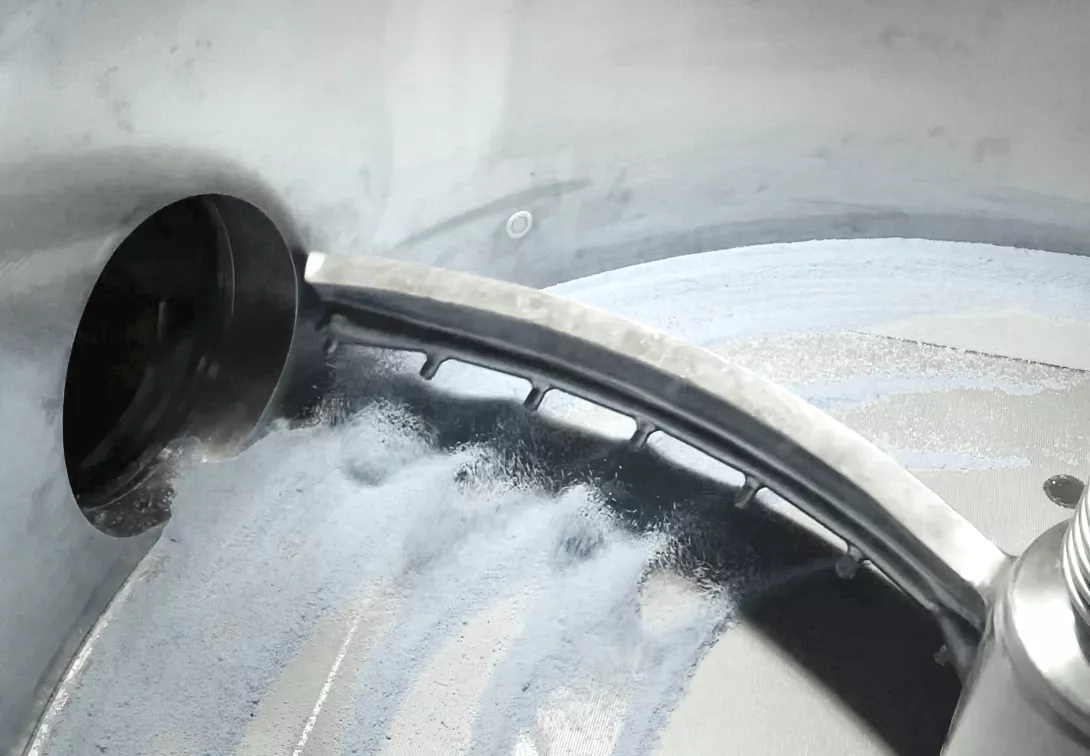
Automatic discharge with Gas knife
Gas Knife is a unique patented technology. The dried heel is pushed with nitrogen into discharging valve, with up to 99% efficiency.
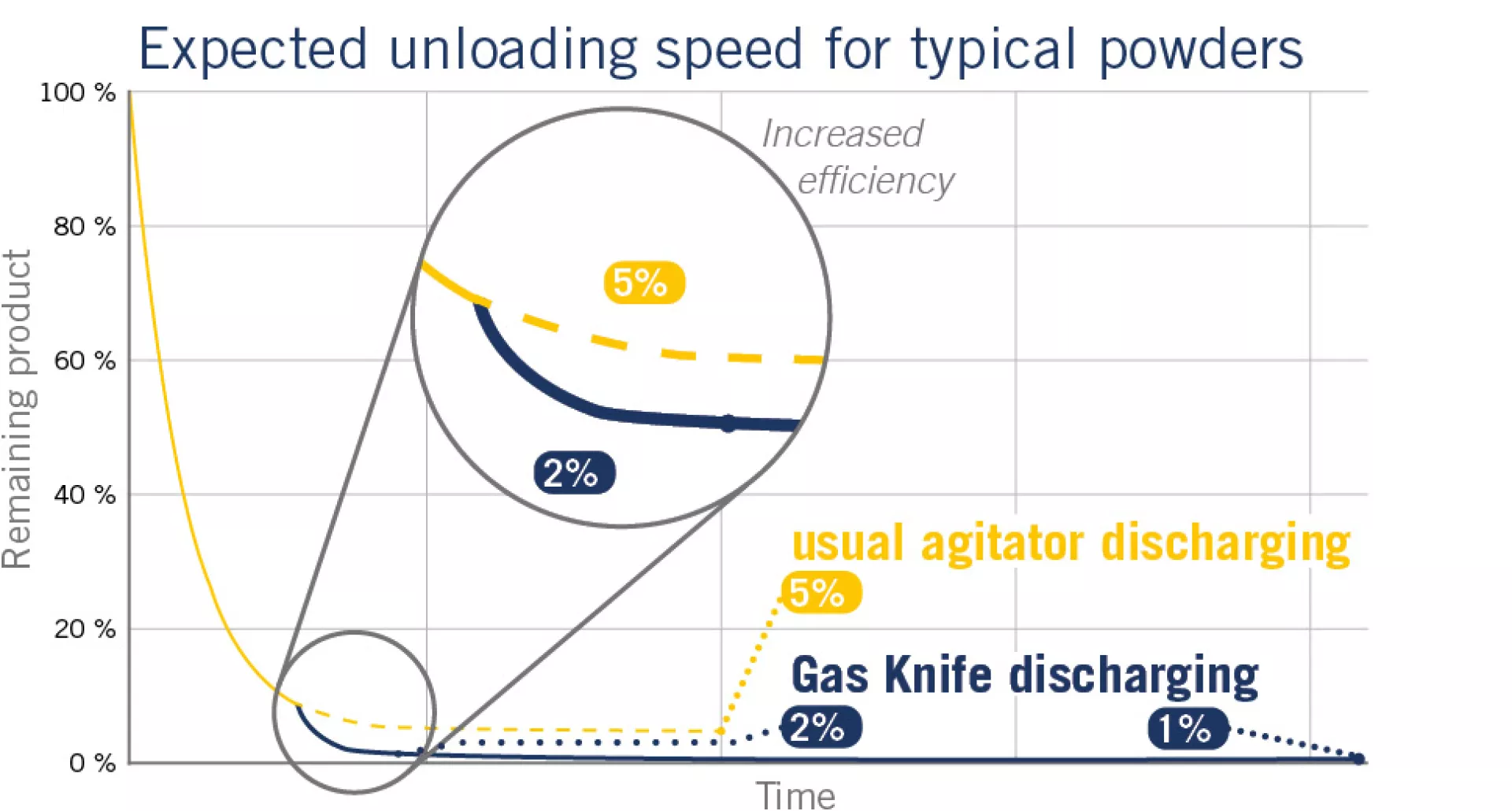
The Gas Knife is also used to improve drying, mixing or dissolution and cleaning.
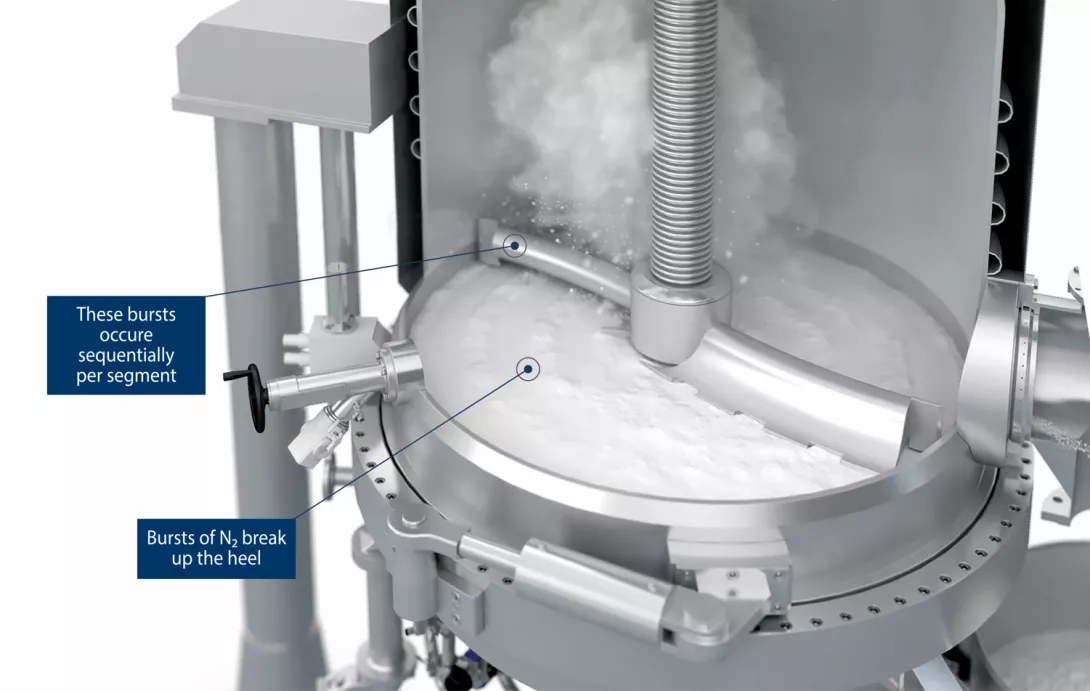
Automatic discharge with Heel Break system
This original option developed by Comber breaks the heel with sequential bursts of nitrogen through the filter media. The optional Whirl Snake turbine generates a flow towards the discharge. It is most effective for powders that form crusts on the media.
Blade Geometry
Blade geometry is crucial to efficiently dry and discharge your product without any degradation.
Blade geometries are selected according to your product needs. With our long experience in Filter / Dryer technologies, our main exclusive designs are:
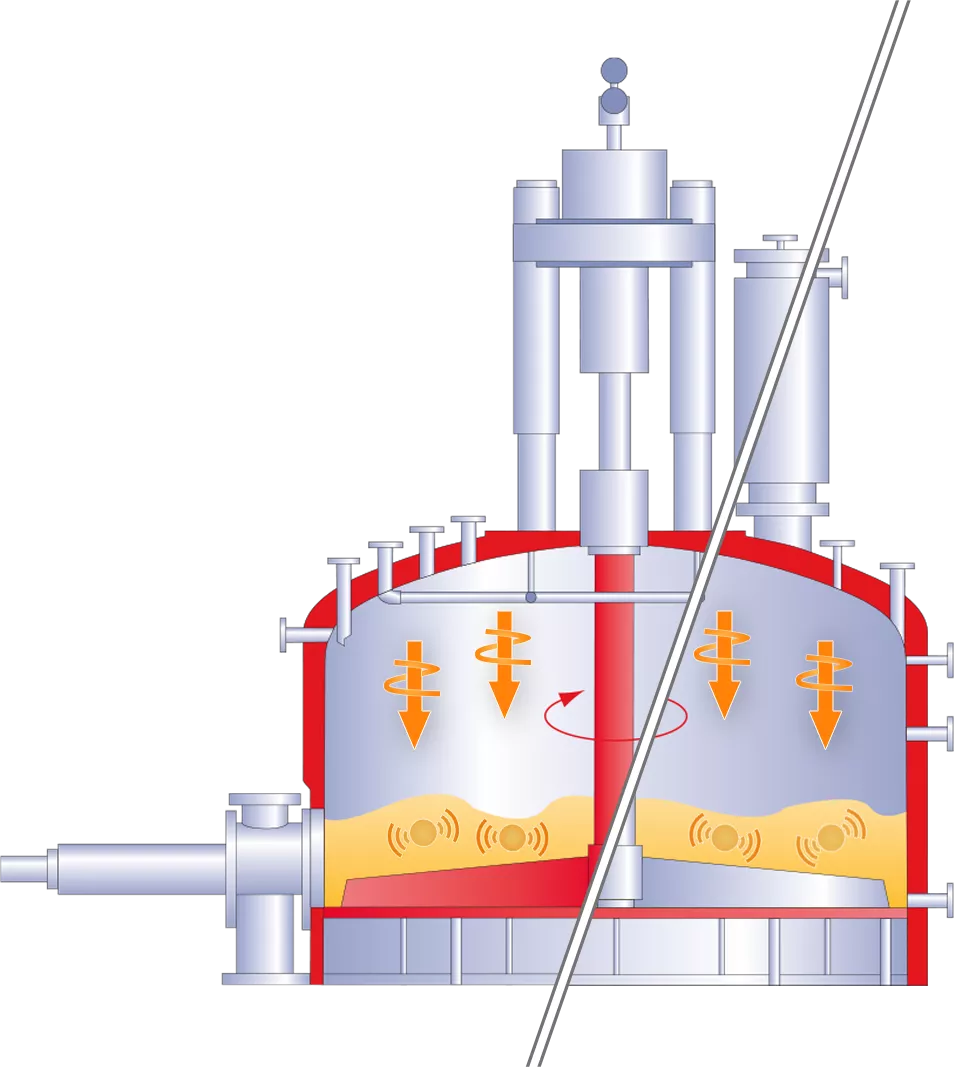
Increased drying efficiency
Optimized drying performance is crucial for the efficiency of the entire operation. De Dietrich Process Systems offers various options to maximize heating and agitation performance to ensure efficient production.
- 15 to 20% faster drying with heated shaft and agitator thanks to 30% increased heat exchange coefficient
- 20 to 25% faster drying with a 3-blade agitator
- Gas Knife option available
- No risk of thermal fluid leakage
- For new equipment or revamping, can be retrofitted for many non‑De Dietrich equipment
Heated shaft & agitator
This is clearly the most efficient option to reduce drying time. This option features an agitator with a thermal circuit that circulates the heating/cooling liquid. As the agitator is welded to the shaft, it prevents thermal fluid from leaking into your product.
Microwave heating
- Recommended in case of high product mechanical sensitivity
- In combination with heated agitator or as a stand-alone option
- Available in trial machine
Need more info?
Our teams are ready to help you!
Documents to download
Request a download
In order to process your brochure request efficiently, we kindly ask you to provide the required information through our form.