Frequently Asked Questions About Charging Solids into a Chemical Reactor
Description
Adding solids into a reactor is a necessary step for virtually all processes in which these types of vessels are used.
Adding solids into a reactor is a necessary step for virtually all processes in which these types of vessels are used. Whether it’s a DDPS glass-lined reactor or one of a different material of construction, almost all include a manway and multiple nozzles to allow access to the vessel’s interior. These access points are used to add solids and liquids to the vessel or serve as installation points for accessories and instrumentation. Since solids come in a variety of shapes and sizes (as well as levels of toxicity, sensitivity, etc.), there are multiple options for introducing solids into a reactor. As a company that has extensive knowledge in both glass-lined reactors and solids transfer, we are often asked about best practices and feasibility when it comes to solids charging, particularly with respect to materials that are difficult to move. Following are some frequently asked questions and points to consider when adding solids into a chemical reactor. While some of these answers are specific to our conveying equipment (our Powder Pump system is designed to be installed on a vessel to safely charge solids into a reactor), a lot of these points are likely applicable to other technologies that are used to mix solids and liquids together.
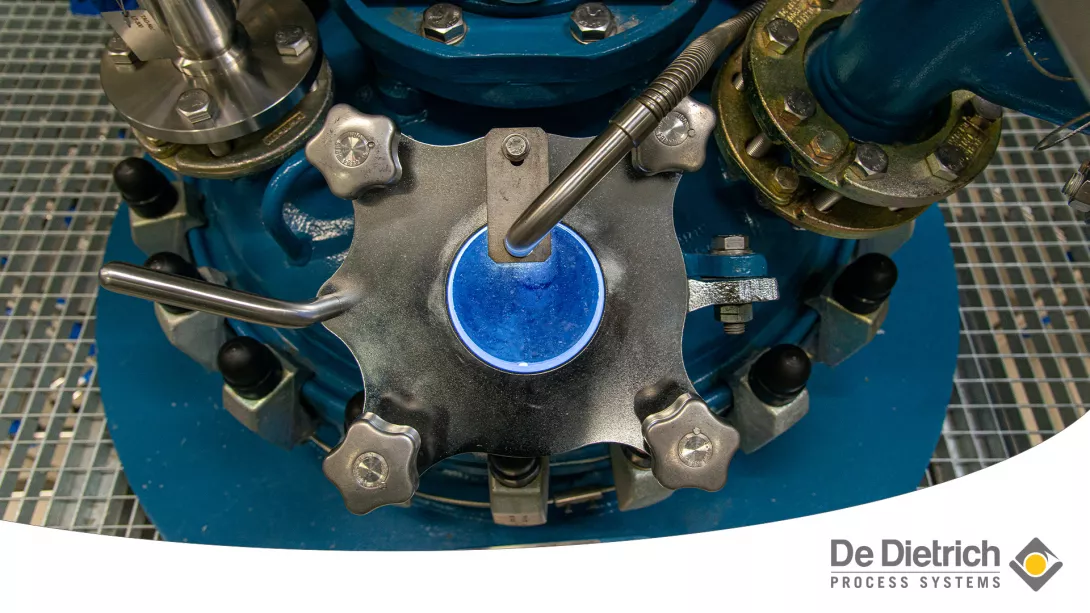
What if I’m handling a corrosive product?
When glass-lined reactors are utilized, it normally means the solvents, solids, and/or their reactive products are extremely corrosive. As such, it is critically important that the Materials of Construction (MOC) of the solids transfer system you employ are compatible with your ingredients and/or product. Some examples of common MOC’s that are used either totally or in conjunction with one another include:
316L SS
Hastelloy C
Borosilicate Glass
Conductive PTFE or PFA
What if my reactor is under pressure?
In some cases, the reactor or vessel may be under positive pressure. This can be an issue when trying to charge material into the vessel from a container at lower pressure. To help ensure no issues occur during material charging, it is important to use a conveying system that can discharge the material into the reactor at a minimum of 5-10 psig over the vessel’s operating pressure. This will help to ensure smooth discharge from a higher pressure zone (solids conveyor) into a lower pressure zone (vessel).
What if I’m charging into flammable solvents?
Explosion or deflagration prevention is the key design intent for many conveying technologies and should be a top priority for yours if you are working with volatile chemicals. For a flame to be created, three things are required: fuel, oxygen, and an ignition source. At DDPS, we focus on two of these components – oxygen and ignition sources. As it relates to our Powder Pump system:
First, prior to any solid being discharged into the reactor/vessel, oxygen entrained within it is dramatically reduced via the vacuum source. Then, the Powder Pump chamber is backfilled with an inert gas, often nitrogen, to ensure the solids have been safely inerted. After that, the material can safely be discharged into the vessel. Watch a video demonstration of the Powder Pump in action to get a visual understanding of its working principles.
Second, to prevent an ignition source (usually in the form of a static electrical discharge), it’s essential that the system is grounded. This is typically the customer’s responsibility to ensure a proper connection is made between the conveying system and a local ground. Some systems, like our Powder Pump, can be designed with anti-static and static dissipating components to help minimize the risk of static electrical build-up and discharge.
What if solvent vapors are condensing in the solids addition nozzle and product build up is occurring?
This is a phenomenon that can potentially cause complications in the process. Hare are a couple of ways we at DDPS have addressed this in the past:
Heat tracing around the nozzle - This can help keep the nozzle area above condensation temperatures of the solvents being used. This helps prevent premature exposure of the solids to liquid solvent droplets during discharge through the nozzle.
Secondary isolation valve with purged spool piece - The secondary valve only opens and closes at the beginning and end of solids charging operations. While it is open, a constant supply of inert gas is supplied to the pipe spool between the isolation valve and the Powder Pump system. This flow of low pressure gas helps keep solvent vapors away from the charge nozzle. This solution is specific to our Powder Pump unit and might not apply to other manufacturers’ solutions. For more details, please feel free to contact us directly.
Is there a way to disperse the material when charging versus dropping in large slugs of material?
Sometimes, discharging relatively large amounts of solids into the reactor one time can make it more difficult to homogenize the mixture before adding the next charge, or possibly overtax the agitator and mechanical seal assembly. To help address this, DDPS provides what we call a “dispersion cone”. It’s an insert that slides into the reactor through the inlet nozzle. When the slug of powder collides with the cone, it helps to better disperse the product in the liquid, making the mixing a bit easier.
What about solids or dust accumulating in my vent line?
Dust accumulation can potentially occur in some smaller diameter vent lines or when handling low bulk density products that don’t settle quickly into the liquid. We can provide a vent filter, which is designed to keep these dusts or solids from getting into your vent line.
De Dietrich Process Systems has extensive experience with not only glass-lined reactors, but also with pneumatic conveying systems, which makes us uniquely qualified to provide answers about this topic. Hopefully, the information we’ve provided in this post answers some of your own questions regarding solids charging into chemical reactors. While we can field any question related to general solids charging inquiries, it’s important to remember that ultimately, every process is different and unique in some way, so don’t be surprised if you still have some unanswered questions. Most of the systems we provide are custom designed to fit our customers’ specific needs. If you have any additional questions or would like to talk more about your application, please don’t hesitate to contact us.