Give a second life to your existing equipment
We refurbish and upgrade your equipment to meet current standards, ensuring compliance and performance equivalent to a new unit. Our refurbished equipment comes with the same warranty as new devices, providing you with reliability and peace of mind. Maximize the lifespan of your equipment while benefiting from a cost-effective and sustainable solution!
Intervention on all kind of equipment
After years of use, some equipment may need refurbishment. If you have equipment that is a candidate for refurbishment, you can rely on us to take care of every step of the cycle (dismantling, refurbishment and upgrade in our workshops, installation and commissioning) in order to deliver you a brand new equipment.
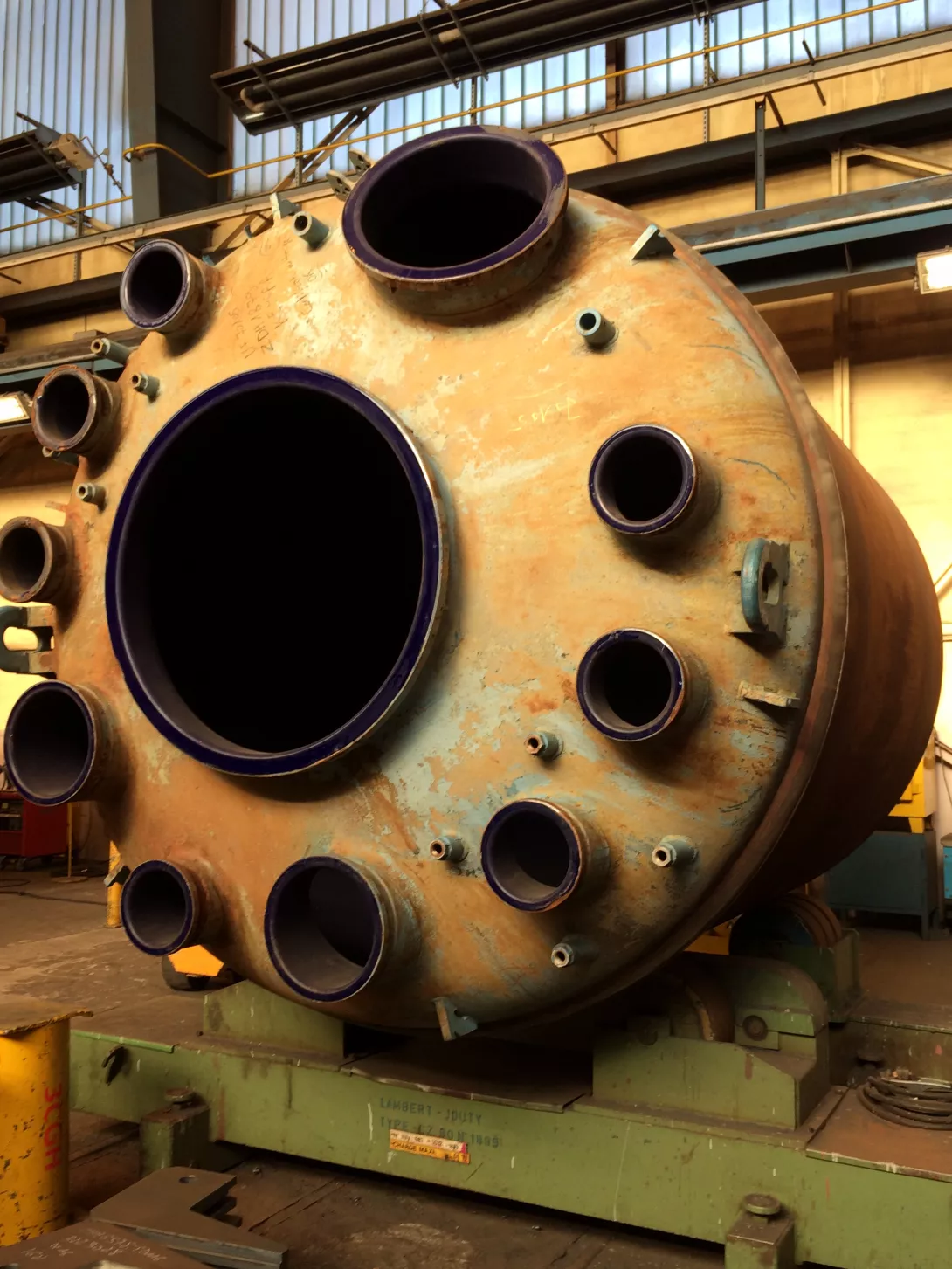
Glass lined equipement Upgrade and Refurbishement
All glass-lined reactors, columns and accessories such as covers, agitators and baffles can be reglassed if the steel substrate is in repairable condition. Reglassing is the process by which older or damaged glass-lined steel equipment is refurbished to a like-new condition. This operation is performed in the nearest De Dietrich facilities, ensuring compliance with industry standards and where it can also be upgraded with advanced technologies, design modifications, or heating system enhancements. We can reglass all equipment, whether manufactured by De Dietrich or other suppliers.
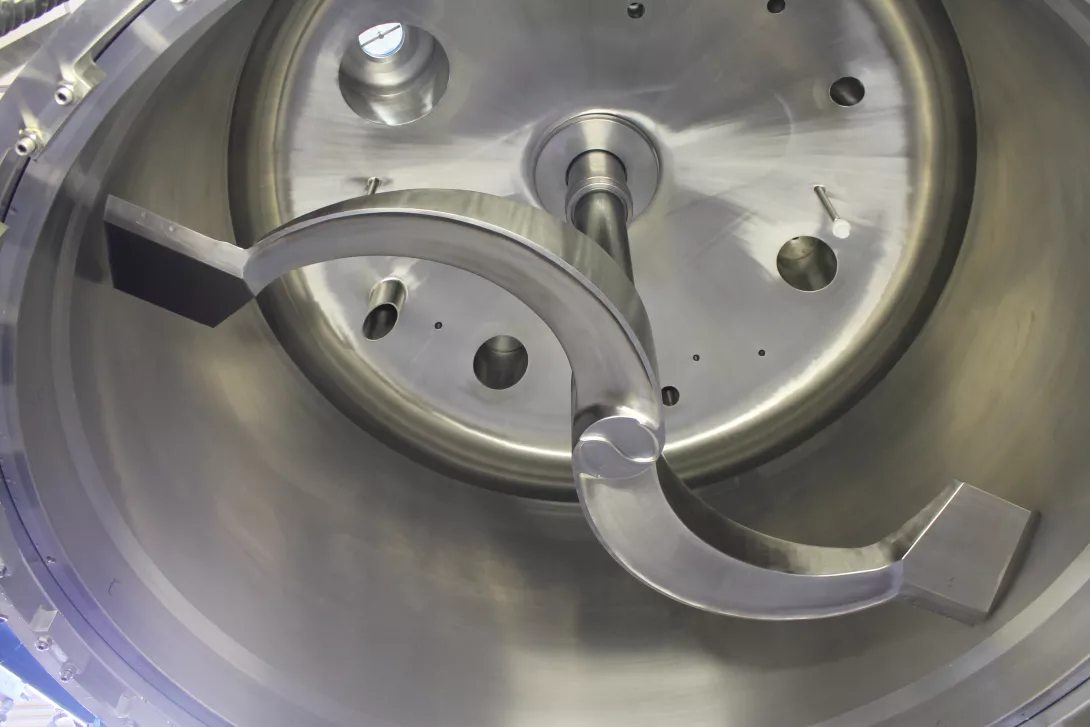
Alloy equipment Upgrade and Refurbishement
All equipment in our product range can be upgraded and refurbished, including filter dryers, dryers, centrifuges, reactors, and columns. We extend the lifespan of your equipment while integrating the latest technologies for enhanced performance. We also upgrade equipment from other manufacturers with our patented, industry-leading solutions.
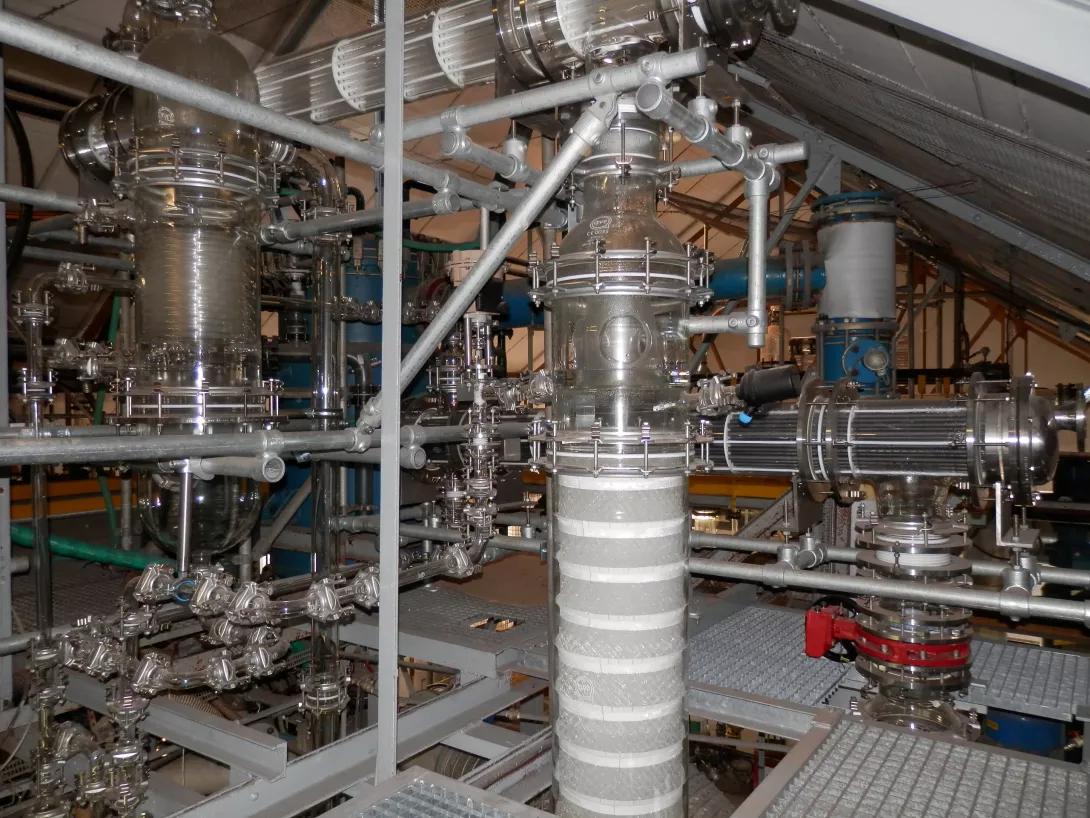
Glass equipment repair
Complete refurbishment of your equipment, replacement of seals & accessories, glass thickness measurement. We can bring your equipment into compliance to meet required standards/certifications (Atex, FDA,…)
Upgrade & Refurbishment Highlights
Economical solution & Delivery time reduced
Possibility to upgrade your old equipment & Same warranty as new equipment
New documentations and certifications provided
Intervention on all brands of equipment
You have questions?
Our teams are ready to collaborate with you and provide solutions for your projects.