Revamping Filter / Dryers to Meet Urgent Deadlines
Claim
Manufacturers of filtration / drying equipment for the chemical and pharmaceutical industries are all experiencing increasing lead times due to a shortage of certain materials, but also due to an overall increase in demand. To remain proactive, upgrading existing equipment, or revamping, is an advantageous solution.
Description
Philippe Giffard, head of after-sales service at the Semur-en-Auxois site (where filtration and drying equipment are designed and manufactured, as well as powder handling and containment) answers our questions about this trend.
In a few words, can you explain the trend around revamping?
Our after-sales service is involved in the supply of spare parts, on-site maintenance, but also the refurbishment and upgrading of existing Filters, Dryers, and Filter / Dryers. This last activity is called revamping. This service has been offered for a long time and is now reinforced by De Dietrich Process Systems for its Nutsche Filter / Dryers for the production of powders in the chemical and pharmaceutical industries.
Revamping increases the performance and reliability of existing Filter / Dryers and/or brings them up to standards without designing a new production system. To improve initial performance and gain productivity, modifications are regularly made to reduce the time spent in the equipment (such as vacuum drying or emptying) or to optimize energy consumption. Other interventions concern the reliability of the equipment to integrate it more easily into a modern industrial tool by meeting the latest safety standards.
Why is this a particularly preferred solution at present?
It is often the best way to meet the customer's real needs. Depending on the project, it is even the most feasiblesolution in terms of time and cost.
Complete revamping is a heavier operation than maintenance or changing systems on the machine. However, the supply difficulties of the last two years have made this operation much more attractive and make it a real alternative to the purchase of new equipment.
But above all, the speed of execution isthe most enticing benefit. Revamping saves a lot of time on the availability of the Filter / Dryer, because we work directly on the functional parts. Depending on the level of reconditioning needed, we can even assemble everything directly at the customer's site, and the production stoppage is negligible compared to the installation of new equipment.
In concrete terms, what is possible?
On existing equipment, we distinguish two main categories ofrefurbishment: those which will allow the equipment to be reintegrated into a modern and safe production system, and those which will allow the equipment to increase its initial performance.
It is difficult to illustrate exactly what the revamping procedure entails because each piece of equipment is unique and requires different repairs and updates , but for the first category of requests, which aims to modernize and make the Filter / Dryers more reliable, we typically address
- Integration of glovebox,
- Upgrade up to safety standards,
- ATEX compliance,
- Cleaning improvement (studies and CIP),
- Modification of the agitator sealing system
- And finally evolution of the automation.
- For the second category, the improvement of performance, our primary goal is to improveproductivity by making the operation faster or more
- efficient:
- Modification of the emptying system,
- Change of the media attachment system,
- Changing the hydraulic power unit,
- Integration of a Gas Knife (De Dietrich Process Systems’ proprietary system to automatically discharge powders up to 99%)
- Integration of heated agitator,
- And even switching from a Nutsche Filter to a Nutsche Filter / Dryer.
From old equipment, we can reach the performance level of new equipment. Especially for drying, which is a key step, you can improve performance and reduce drying time by 25% with the simple addition of heated agitators.
Everything is possible regardless of the equipment?
The good thing is that we work on De Dietrich Process Systems Filters, Dryers and Filters / Dryers, including the historical brands Guedu and Rosenmund, as well as other designs (Mavag, Cogeim, EfCI...).
However, each machine is different, and an initial examination is necessary to know if the revamping will be beneficial. Fortunately, even for equipment from other suppliers, more than 60% of requests are viable candidates for refurbishment!
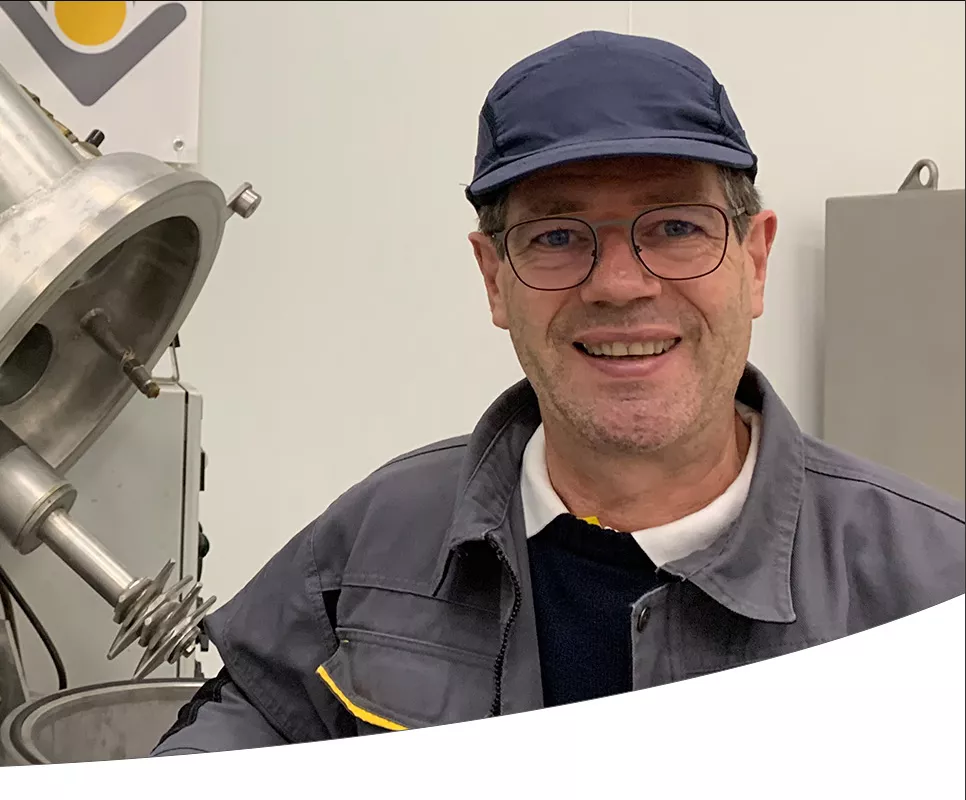