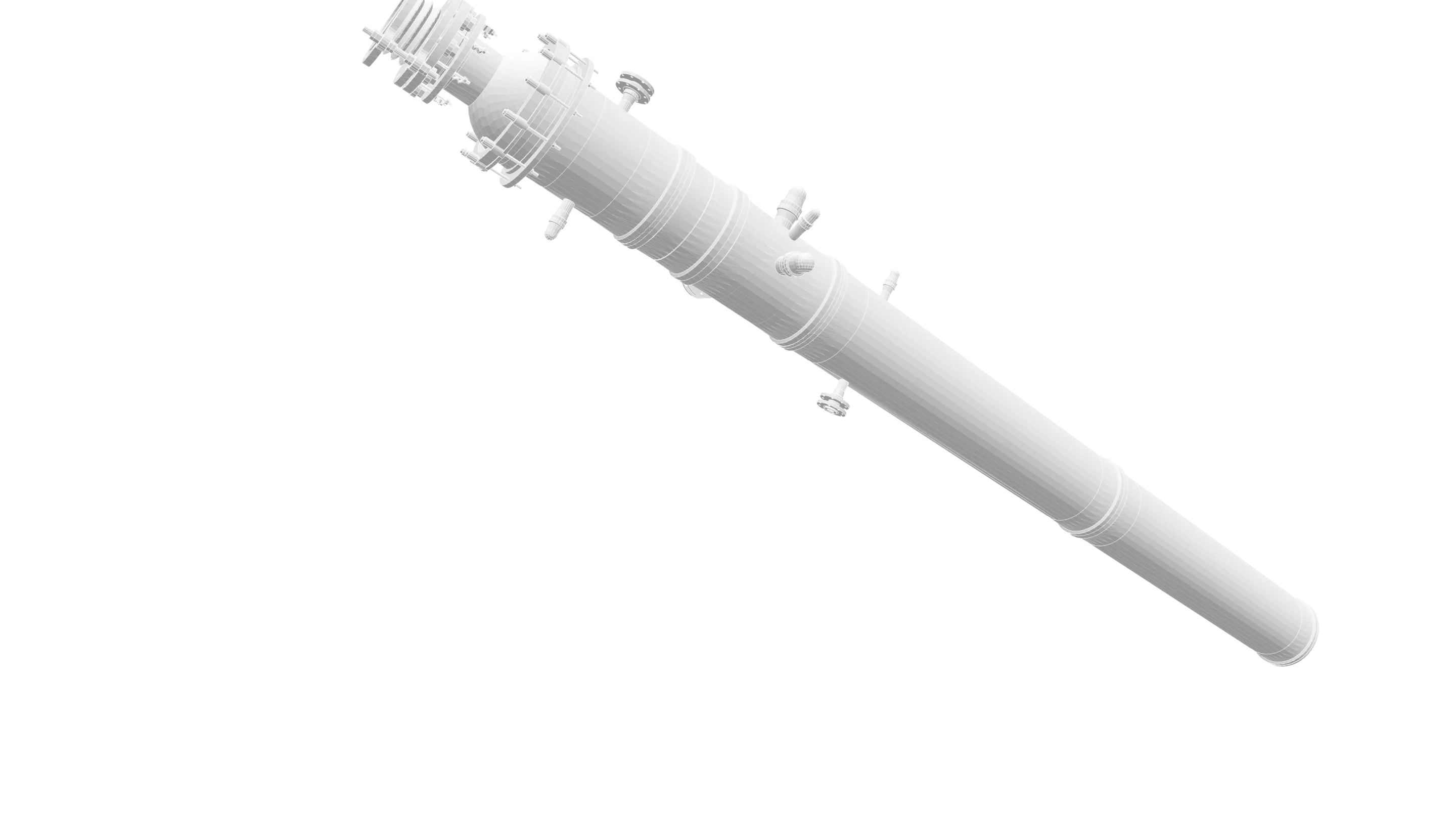
Separation columns
Process Solutions for thermal separation
Columns and internals for aggressive media
Optimal solutions using separation columns for highly corrosive processes
Thermal separation processes are often used in treating and cleaning chemicals. Very common are processes that involve two liquids or a liquid and a gas. The processes used mainly involve extraction, absorption, desorption or stripping, distillation or rectification.
The process core in the columns consists of packings that provide the mass transfer surfaces; these involve specialised trays such as bubble-cap or sieve trays as well as random or structured packing. Especially for random and structured packing and in addition to support trays further internal components are required to wett all surfaces equally for optimum mass transfer. These additional components include liquid distributors that evenly distribute the incoming fluid over the column cross-section, and wall wipers to deflect liquid from the wall inside the column back into the packing. Further internal components are needed to control the liquid flow out of the column; demisters reliably restrain droplet drift at the upper end of the column, while collectors underneath the packing catch the reflux liquid, either removing the liquid from the column or feeding it back to a redistributor. Vortex breakers and collectors at the lower end of the column ensure reliable liquid drainage. For optimum process performance the designs and materials vary widely for differnent processes and nominal column widths. These constructions have been developed over decades and have proven their worth in our QVF® processes.
We would be pleased to design a column and select internal components optimised for your application.
From basic engineering to start-up, we provide everything from a one-stop shop.
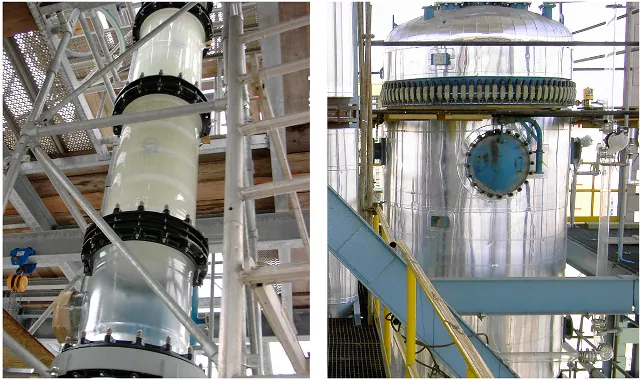
Separation columns
Glass and enamel columns
Separation Columns Key Figures
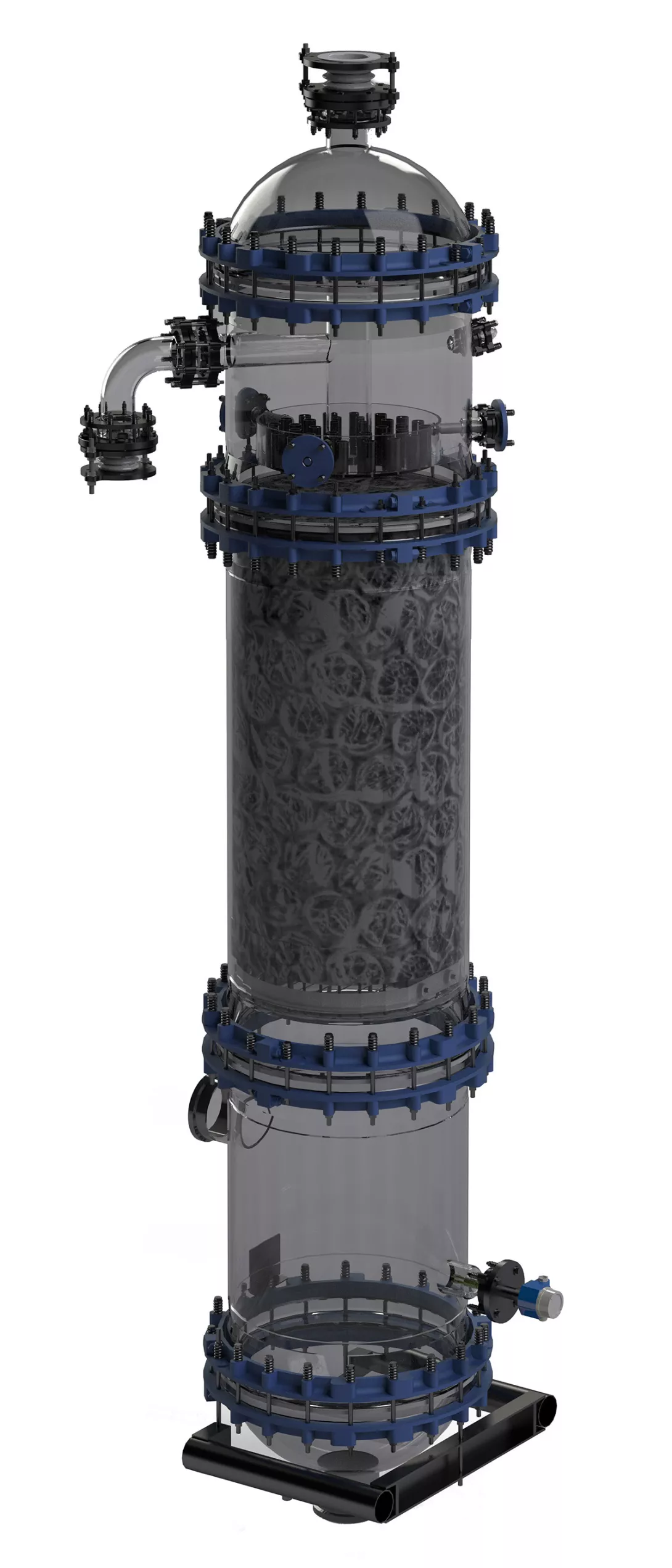
Our Glass Columns include :
- Bubble cap trays, the ideal solution for a wide range of loads
- Packing, for a guaranteed compatibility
- Structured packing for high separation efficiency and a low-pressure drop
- Wall wipers / guiding funnels, PTFE strips to boost efficiency
- Support grids, glass to carry the whole load securely
- Patented QVF® core-trays
- Liquid distributors, uniform wetting for any load
- Collectors for reliable side drainage
- Demisters and mist eliminators, no droplet entrainment
- Vortex breakers, outlet collectors, vapour-inlet for reliable draining
CONCEPT - DESIGN - ENGINEERING – IMPLEMENTATION
One-stop shop, quality in one hand
We have decades of experience in supplying column systems for thermal separating processes, especially those involving highly corrosive media like acids. We design and manufacture the main components according to national and international quality standards and directives. The separation processes have been developed in our own test hall. Hence we have our own high expertise in designing separation processes and, if requested, we will provide process guarantees. We would be pleased to engineer for you based on a computer simulations the most suitable column for your application, an optimum solution to operate your process reliable and efficient.
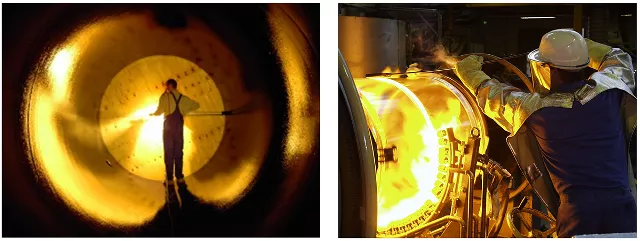
Production of a column section made of enamelled steel / Production of a column section made of borosilicate glass 3.3
We deliver QVF® columns in borosilicate glass 3.3 up to DN1000 and De Dietrich® glass-lined steel columns up to DN2400. Our columns operate at temperatures ranging between -60° and +230°C. We design QVF® glass columns and De Dietrich® glass-lined steel columns according to the 2014/68/EU (97/23/EC) according to AD-2000 or DIN/EN-13445) pressure vessel standards and directives for the European market, and the standards applicable such as ASME VIII Div.1 for the USA or SQL for the Chinese market for glass-lined columns. QVF® glass columns according to EN1595 are approved for pressures between -1 and +1barg, and De Dietrich® steel and glass-lined columns are usually approved for pressures between -1 and +6barg. We also supply columns for extended application scenarios on request.
Both materials used – De Dietrich® DD3009 glass-lining and QVF® borosilicate glass 3.3 – are extremely resistant against acids, providing a cost-effective and temperature-resistant alternative to special metallic materials and non-vacuum-resistant PTFE-lining.
The surfaces of both materials are inert and extremely smooth, cutting the risk of caking while facilitating the cleaning process. Both materials are catalytically inert and neutral to taste.
Our unique manufacturing process ensures leading global tolerance accuracy in smoothness, straightness and roundness. Glass-lined columns are available at tolerances to ½ DIN 28007-T2 on request. Our glass-linings fulfill current standards such as ISO 28721-1 on quality and quality assurance.
The tray, liquid distributor and collector heights in addition to column section heights for the random or structured packing play an essential role in overall column height, which is often restricted to certain total for structural reasons. We manufacture segments at max. 5.5m height for glass-lined columns that can reach a overall height of 52m.
QVF® PROCESSES
Systems for highly corrosive process applications
Mineral Acids
H2SO4 Recovery
HNO3 Concentration
Cleaning
Denitration
HCl Concentration
Dilution
Halogenes and halide media
Br2 and bromides Production
Cl2 and chlorides Cleaning
l2 and iodides Removal
Recovery
Waste gases
NOx Conversion
SO2 and SO3 Absorption
HCl and Cl2 Reduction
Removal
Cleaning
You have question?
Our teams are ready to collaborate with you and provide solutions for your projects
Documents to download
Request a download
In order to process your brochure request efficiently, we kindly ask you to provide the required information through our form.