QVF® Shell And Tube Heat Exchangers
Versatile, corrosion-resistant and transparent
The QVF® coil heat exchangers can condense, vaporise and temper highly corrosive media between -80 and +200°C.
The QVF® SUPRA shell and tube heat exchangers are available with
- nominal diameters of DN80 to DN300
- heat exchange surfaces of 0.3m² to 27m²
- tubes made of borosilicate glass 3.3 or SiC
- shells made of borosilicate glass 3.3, glass-lined steel or stainless steel
- headers made of borosilicate glass 3.3, glass-lined steel or stainless steel
The standard models of the QVF® SUPRA shell and tube heat exchanger are designed for the condensation and tempering of highly corrosive substances between
- -20 and 150°C
- -1 bis +6 barg
Heat Exchangers

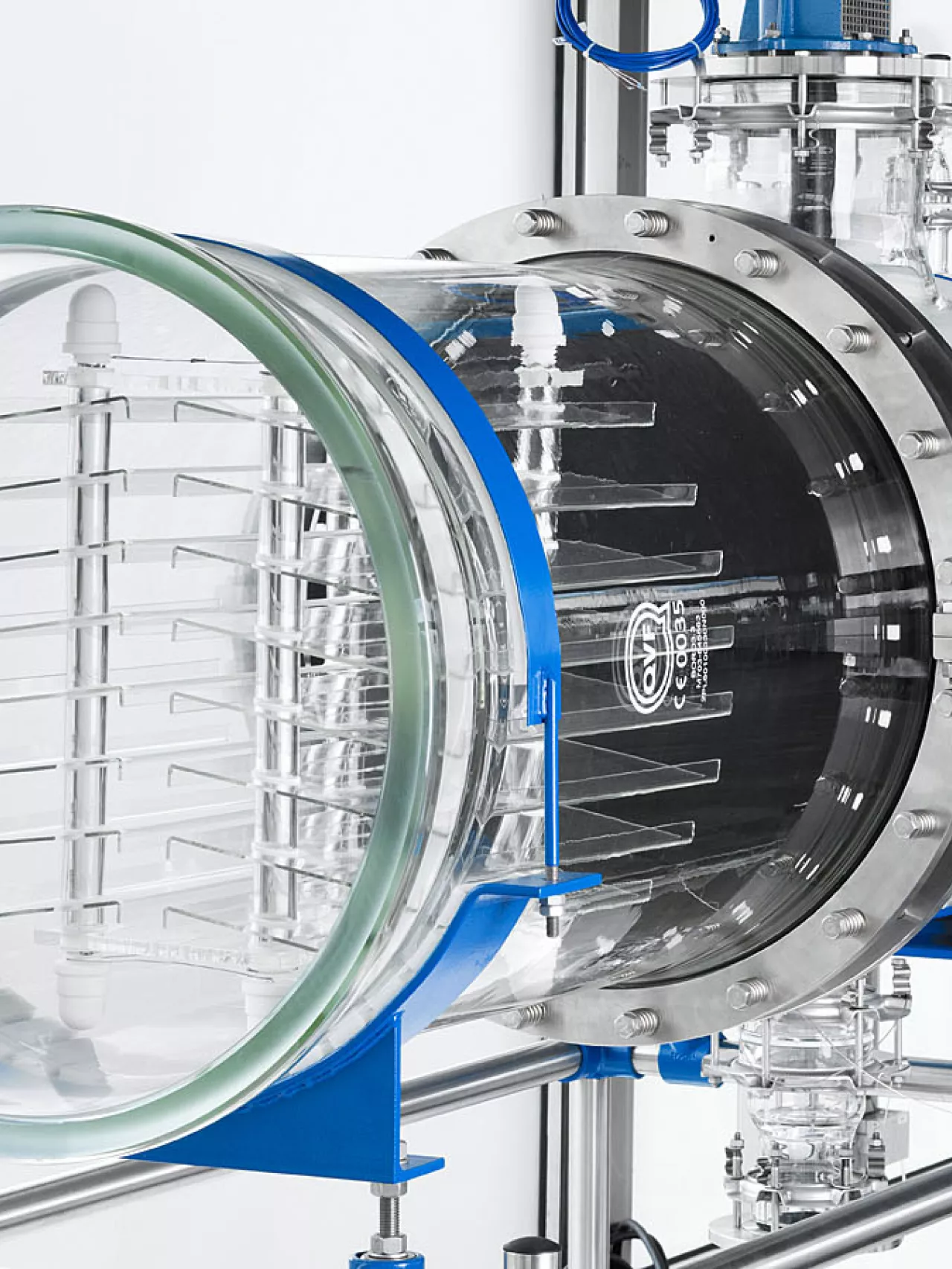
One-piece all-glass component without sealing points
QVF® coil heat exchangers made of borosilicate glass 3.3 are one-piece, as the coil is fused to the jacket and there is therefore no sealing point. Cross-contamination between the service medium and the product is therefore impossible. These all-glass heat exchangers can be ideally integrated into glass apparatus and are just as easy to operate and clean as the other components of the glass system. The pressure of the service medium can be a maximum of 3barg. The maximum pressure in the glass jacket depends on its diameter and corresponds to that of other glass components of the same nominal diameter. The maximum temperature difference between the service medium and the product is 180°C at a maximum of 200°C. The extremely smooth glass walls provide hardly any grip for possible contamination, so that the heat transfer remains constant over long periods of time. The QVF® coil heat exchangers are available in various designs from 0.03 to 15m² and are ideally suited for a wide range of processes such as temperature control, condensation and evaporation. If larger exchange surfaces are required or the pressure or pressure drop of the service medium in the coil is higher than 3barg, QVF® shell and tube heat exchangers are the right choice.
The QVF® SUPRA shell and tube heat exchangers highlights
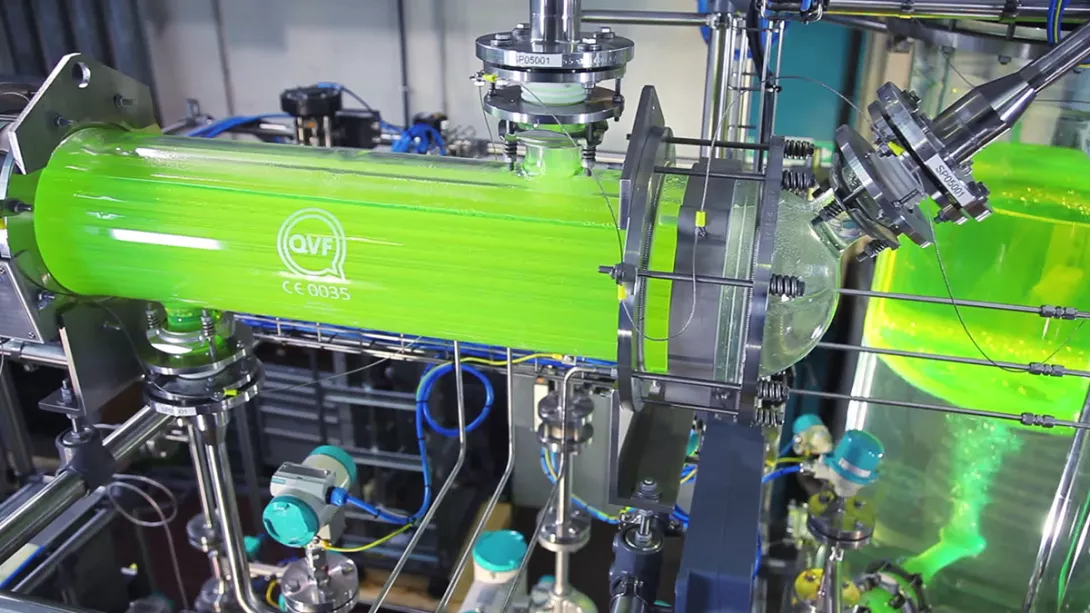
- Corrosion and diffusion resistant materials
- For pressures up to +6barg
- Modular design catering for a wide range of heat transfer processes
- One tube diameter for all versions
- One tube fitting for all versions
- One PTFE tube plate for all versions of same nominal diameter
- FDA material certificates for all components that are in direct contact with the product
- Prevention of cross-contamination by means of optional intermediate chamber that can be drained separately
QVF® SHELL & TUBE HEAT EXCHANGER HIGHLIGHTS
The modular system
Up to DN300 with 27m² heat exchange area
1 up to +3 barg on process side, +6 barg on service side
Tubes made of glass or SiC, Shell made of glass-lined steel, glass or steel. Tube plate and sealing bushes made of PTFE
Optional cGMP design
You have question?
Our teams are ready to collaborate with you and provide solutions for your projects
Documents to download
Request a download
In order to process your brochure request efficiently, we kindly ask you to provide the required information through our form.